What is Mixed-Model Production?
By John Wright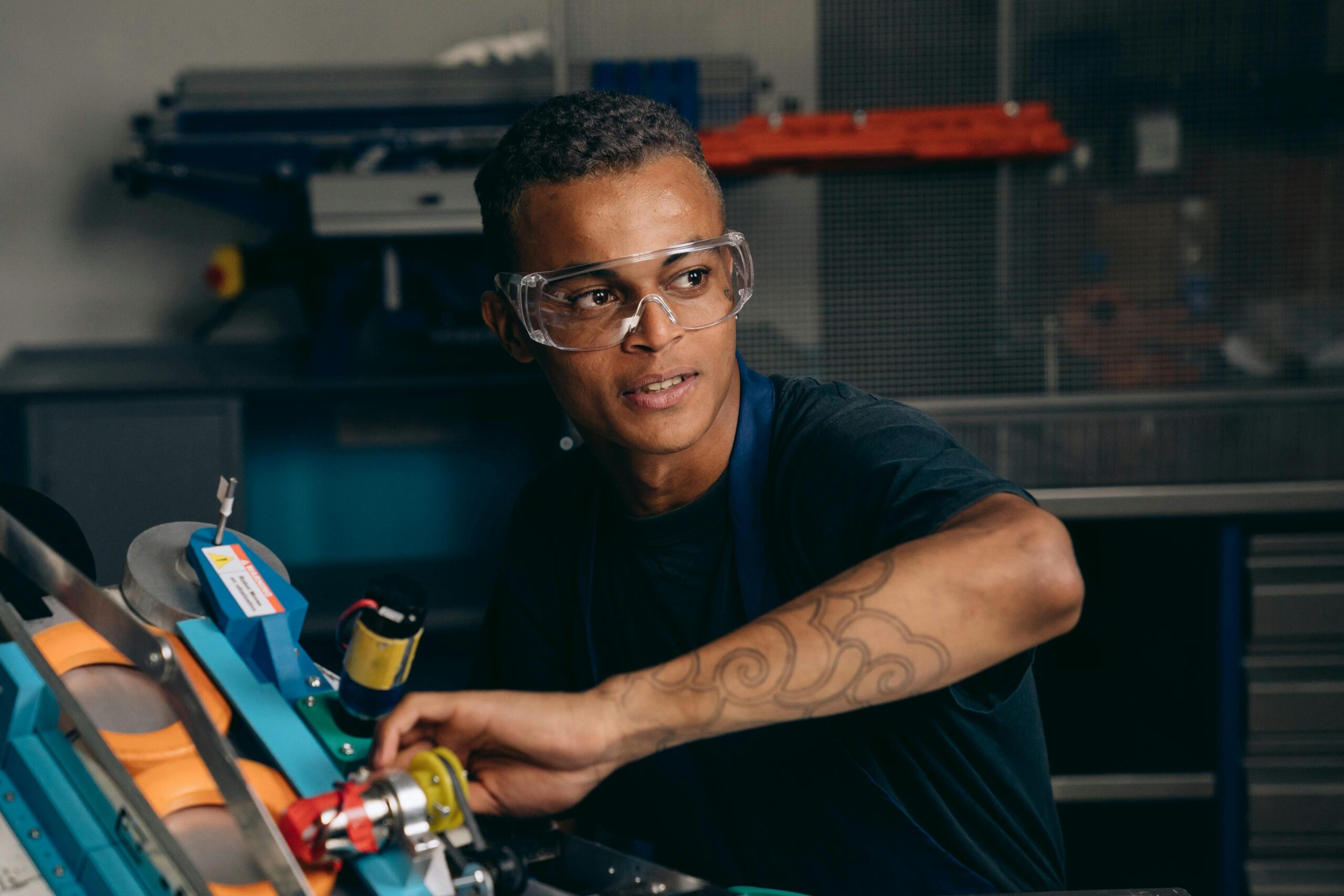
Mixed-model production (MMP) (or mixed-model assembly) is defined by the production of various products and product variations on the same assembly line. While assembly lines might have started with Henry Ford’s famous quote, “Any color the customer wants, as long as it’s black,” mixed-model production is a response to ever-expanding demand for variety, novelty, and customization.
This type of production is also sometimes known as discrete manufacturing, as we mentioned in a previous insight. However, some experts consider discrete manufacturing any form of production where each item is tracked individually, including job shop and additive manufacturing processes.
As Richard Rahn, Co-Founder of lean manufacturing consultancy Leonardo Group Americas, writes, “mixed-model assembly is the ability to assemble a family of products that share similar processes, similar work content, and similar materials, on the same production line, with high productivity, high quality, and high flexibility.”
Rahn should know – mixed-model production and lean manufacturing both emerged from the Toyota Production System and feed into manufacturing continuous improvement processes.
To see it in a simple visual format, check out the graphs below:
Traditional assembly line production, with breaks to change over the line between runs
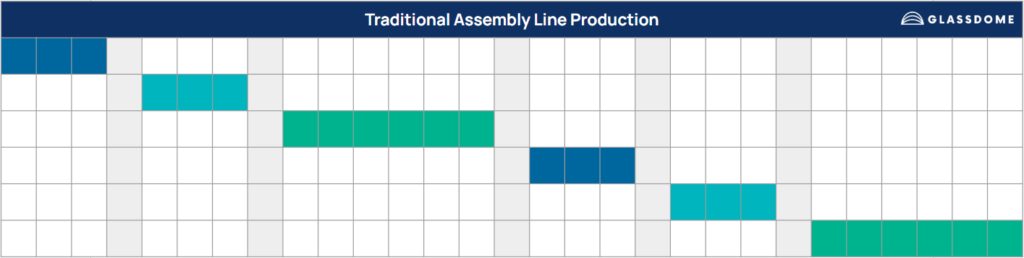
Mixed-model production, with varied products continuously moving through the line
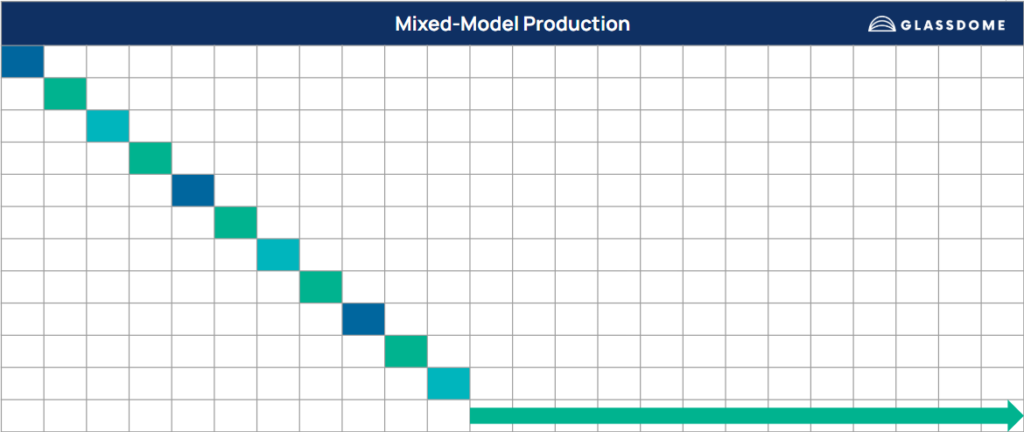
What are the benefits of mixed-model production?
In an ideal world, MMP allows for a more flexible, efficient, and green production process.
Flexibility is an obvious benefit. If demand is variable, MMP can easily handle the job. Customer demands are met quickly as new orders flow seamlessly into the queue, instead of waiting for the entire line to change over. This enables just-in-time production and cuts down on inventory storage costs.
Manufacturers also often see increased efficiency. Capacity is automatically allocated to products with high demand. Using the same line and equipment reduces changeovers and downtime. By cleverly arranging the production schedule around product variations, plant managers can ensure that as much of the plant’s equipment is being used as possible, even with multiple products moving at the same time.
Finally, MMP is usually greener than a proliferation of assembly lines. By producing everything on the same line, companies can more intensively and intelligently use inputs, cutting down on waste and disposal costs. Reduced downtime and changeover time through combined, much busier, assembly areas, combined with the smaller area required for their production, means less energy is used per product.
What are the challenges of mixed-model production?
Put simply, it’s more complicated. Single-product assembly lines are a comparatively simple management task.
Instead of a single process with defined inputs, steps, and outputs, managers must deal with a wide range of inputs, processes, and outputs.
MMP requires thought and flexibility in inventory, setup, training, tracking, parts management, and production scheduling.
And if your line has a stoppage, you’re in trouble across the board, not just for one product.
How can my company implement and improve mixed-model production?
The key to MMP is visibility.
If they can see their facility clearly, plant managers can schedule production effectively, respond to issues quickly, and plan for the future accordingly.
Initial implementation requires an audit of all of the possible items that can be produced on the same line, and what goes into producing each one. This means getting a grip on your production process, machine effectiveness, and workforce capabilities and availability. To help them do so, many operations managers use techniques like the 4M Method.
Once that’s done, you need to create a single source of truth for your production team. Your plant is full of useful data. It can tell you what you need to do and when you need to do it, as long as you have the ability to wake it up and put it to work.
A shared platform pulling real data from your factory allows effective communication, quick problem solving and unified goal setting.
That’s where a solution like Glassdome comes in. The Glassdome Production Monitoring platform helps MMP plant managers see, improve, and report on their production in real time.
With real-time production monitoring, advanced data analytics, and tailored improvement strategies, you’ll have the tools and expertise you need to enhance every facet of your operations using the data you already have.
Accelerate mixed-model production at your facility
Speak with a Glassdome manufacturing expert to learn how