The Five (or Six) Types of Manufacturing Processes
By John Wright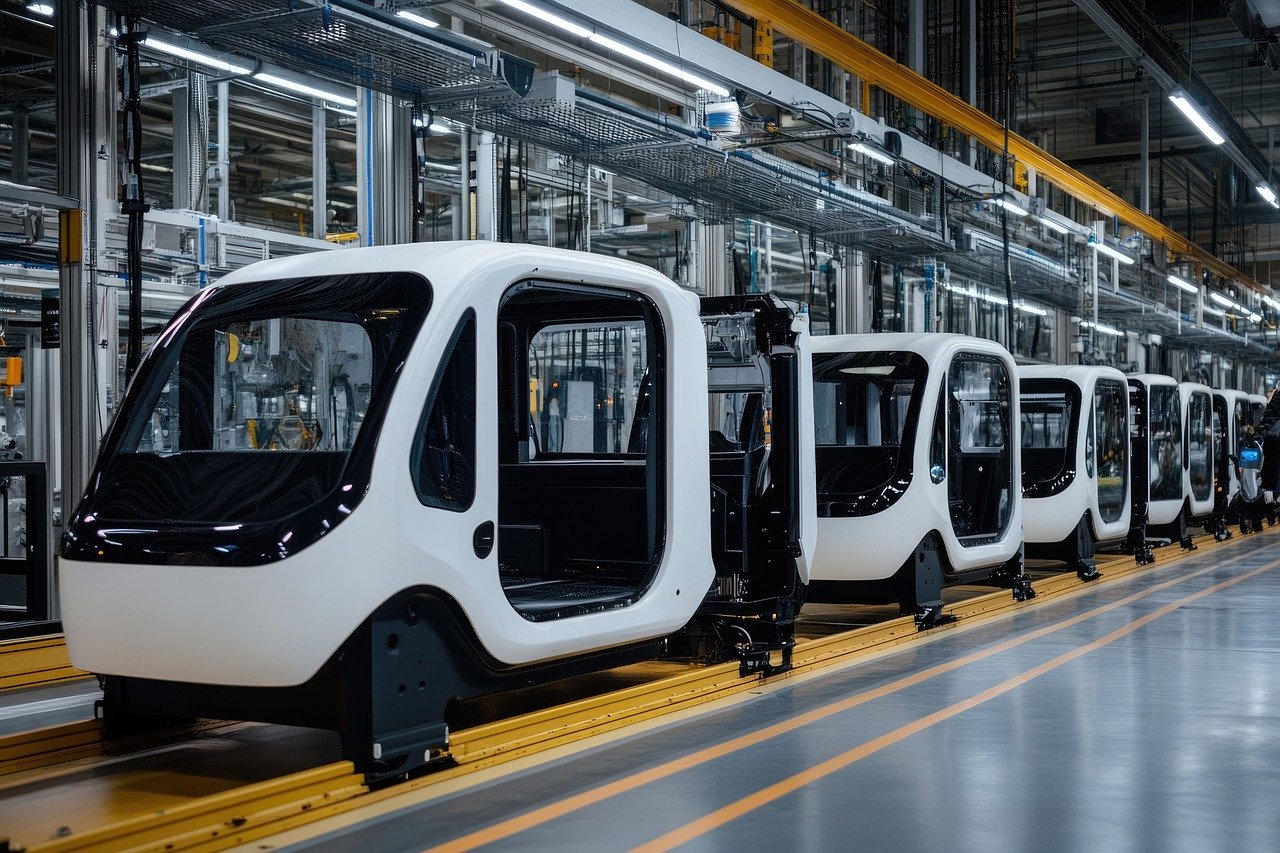
Although each factory can feel as unique as a snowflake to its managers, there are widely considered to be five or six types of manufacturing processes: Job shop, repetitive, discrete, batch, and continuous manufacturing are the classic five, and additive manufacturing is sometimes included.
Need to customize each item? Job shop, discrete, and additive manufacturing are the processes for your business.
Make the same product over and over at a fast rate? You’re probably using repetitive or continuous manufacturing.
Require flexibility switching between groups of identical products? You might be using batch manufacturing.
Need more detail as you develop your own manufacturing strategy? You’re in the right place. Let’s dive in.
1: Job Shop Manufacturing
In job shop manufacturing, products move through workstations or production areas instead of down an assembly line. At each stage, workers receive the product, complete an action, and move the item to a new area. In many ways, it’s the original manufacturing process, dating back to the era of craftsmen and guilds.
Job shop manufacturing is ideal when products require unique methods or sequences of steps. It’s great for companies that sell customized products in small quantities.
The tight focus on each item also gives it an edge in quality control (or at least it’s supposed to), as its slow pace and tight focus gives workers time to find and fix flaws.
Often used for: Specialized aviation and marine components, high-tech industrial machinery, luxury consumer goods
2: Repetitive Manufacturing
In repetitive manufacturing, products are mass-produced using identical steps on an assembly line. If job shop manufacturing calls to mind a medieval guild, this is Henry Ford.
Repetitive manufacturing is fast, stable, and efficient, satisfying a committed production rate and is perfect for products with consistent customer demand.
However, production faults magnify quickly as they are repeated over and over again before they’re noticed (unless you have quality visibility through a tool like Glassdome), and adaptation requires shutting down and reworking the line.
Often used for: Electronics, toys, confectionery
3: Discrete Manufacturing
In discrete manufacturing, products move down a production line, but there are variations within stages to allow workers and machines to modify the products as they proceed through the process. It is in some ways the midpoint between job shop and repetitive processes.
The “discrete” in the name comes from the idea that the process views each product on the assembly as an individual item with its own specifications. At its best, it combines the speed and efficiency of repetitive manufacturing with the customization of job shop manufacturing.
However, the coordination required to maximize product flow through a discrete process, with so many unique steps and varying times at each station, is a considerable challenge. The interlocking systems really do need to run like the gears in a clock or the whole plant suffers.
(The Glassdome Production Monitoring platform is useful in any factory environment, but this is where we find we provide the most value. Visibility, problem-solving, and report automation give plant managers the tools they need to make it all work together.)
Often used for: Clothing, automotive, firearms, medical devices
4: Batch Manufacturing
In batch manufacturing, a factory makes a set of identical products, then resets production to make a different set of identical products, much like a baker making batches of cookies.
As orders come in, manufacturers can handle the full order in one batch, then clean and prepare their equipment for the next order. It is easy to automate and highly flexible order-to-order, but completely inflexible within each batch.
It’s especially useful for types of production where raw materials need to be blended together to create a new product.
Often used for: Food & beverage, pharmaceuticals, plastics
5: Continuous Manufacturing
In continuous manufacturing, raw materials like gases, liquids, powders, and granules that literally flow through the process. As constant movement is required for the chemical reactions or changes to occur properly, manufacturing must continue 24/7 or it does not work.
By nature, it’s used to make products that require chemical reactions or similar types of molecular change.
Often used for: Oil refining, Fertilizer production, chemical processing, pharmaceuticals
6: Additive Manufacturing (or 3D Printing)
Additive manufacturing was once considered the newest addition (get it?) to the five types of manufacturing processes. In additive manufacturing (also known as 3D printing), a digital model of the product is created, and material is added layer by layer to create the product.
This is the newest and most niche type of process. First, the digital model is created, either with design software or through a simple scan of an existing product. Next, the 3D printer builds up the product using malleable materials like plastic or metal.
With 3D printing, manufacturers can create items that conventional manufacturing methods literally can’t make. AI optimization can help ensure that their fantastical shapes will be structurally sound. However, it’s a slow, expensive process. Much like job shop manufacturing, it suits industries that require customization and demand higher prices.
In fact, while there was an initial burst of excitement that led to its inclusion in many of these lists, in its current stage of development it is so cumbersome and limited to certain materials that it is falling out of favor with most serious manufacturers, leaving the original five types of manufacturing processes.
Often used for: Medical devices, firearms, cosmetics, shoes
Which method is right for my business?
There is no “correct” one of the six types of manufacturing processes. Each manufacturer decides based on a combination of the materials, budget, quality, volume, and size of the product.
Whatever method you use, you need to have visibility over your process, and the ability to find, fix, and report on what’s going on in your facility. That’s where Glassdome can be helpful. Giving you accurate process data, and presenting it in custom dashboards that tell you what you need to know, when you need to know it.
Interested in learning more about Glassdome Production Monitoring Software?
Get in touch with one of our manufacturing experts.