What can Manufacturing Operations Management Software do for Food & Beverage Manufacturing?
By Max Krevitz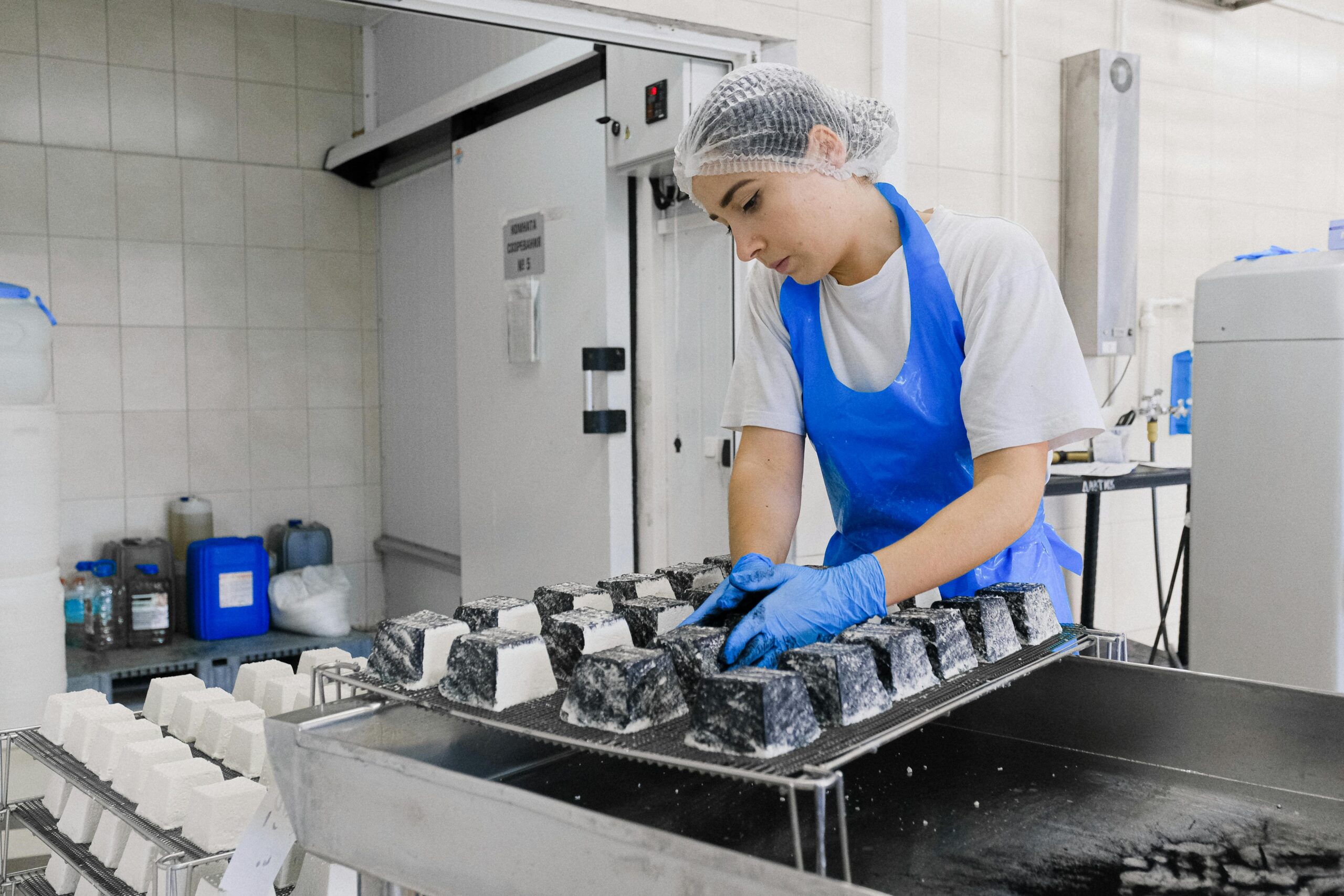
Food and beverage manufacturing professionals crave high quality, predictable output with little variance and need software to help them do it. So customers can find the treat they’re looking for, and get exactly what they want every time they take a bite or a drink. When that happens, they come back for more.
Executives, engineers, and managers know what it takes to achieve that goal. They need visibility in what’s happening on the floor. They need to maximize their machinery. They need information presented in a usable way. And they need it all to come without a huge investment in time, money, and stress.
That’s where manufacturing operations management software like the Glassdome Production Monitoring platform comes in.
Challenges
In many food and beverage production facilities, decreasing downtime and increasing quality takes months.
On the floor, islanded equipment confines visibility to local displays. Production status, logs, and KPIs are written down on whiteboards and paper. Analytics and reporting are done manually, or rely on slow, error-prone data entry.
A dwindling skilled labor pool and difficult training environment only amplify production uncertainty headaches.
Executives struggle to balance short-term profitability with long-term sustainable growth, and do it all without any real-time visibility into the causes of downtime and inefficiency. Out-of-data and imperfect data leads to slow, flawed decision-making.
What is Manufacturing Operations Management Software?
Manufacturing operations management software (MOMS) is a clear, simple platform that helps manufacturers see, improve, and report in real time. With a properly implemented MOMS system, you get full visibility into your manufacturing processes, which helps you improve your manufacturing performance in an informed way.
MOMS brings all of your machines and processes together to help you become more efficient and flexible and get to market faster. With a MOMS system, you’ll be able to quickly respond to changes in the market.
How does Manufacturing Operations Management Software help F&B operations?
MOMS helps food & beverage production facilities in four distinct ways: increased output, improved quality, better preventive maintenance, and connected batch processing.
Increased output
First, and most obviously, implementing MOMS helps you increase output.
With real-time visibility, you’ll cut downtime and avoid bottlenecks. When a machine is down or underperforming, you’ll know right away. And if your MOMS system has machine and operator reporting (like Glassdome does), you’ll know exactly what happened.
That way you can quickly find out what happened and fix it for the future.
Improved quality
MOMS helps you improve the quality of your output. That leads to fewer finished products rejected for low quality, and increased customer satisfaction.
The software platform does this by aggregating and analyzing all of the data from your factory floor. Instead of relying on slow trial-and-error fixes, you can see where issues arise and fix them before your next batch. Correlation analysis also helps you confirm the degree of influence each issue and fix has on the final product.
Better preventive maintenance
MOMS helps you take better care of your machines, while using limited man-hours more efficiently.
Many factories maintain machines on a schedule, because it’s impossible to know exactly how many hours a machine has been running. Barely used machines get premature service, while hard-working tools don’t get what they need. The visibility that comes with MOMS allows for usage-based maintenance, so machines get maintained exactly when they need to be.
Visibility through time also allows you to see any performance degradation as it happens, so you can make timely small adjustments instead of late costly revamps.
Connected batch processing
Many food and beverage products are made in batches, which need to move through disconnected systems. When something goes wrong in one machine, it results in significant added cost in waste material and lost production time.
The Glassdome MOMS platform specializes in batched, continuous batched, and hybrid manufacturing processes. Our wireless connectivity and cloud-based model make it the ideal solution for a process that is disparate by nature.
MOMS in Action
Challenge
A global confectionery manufacturer wanted to improve the consistency of its products. Specifically, it wanted to minimize variability in product size and thickness.
Existing Process
Size and thickness of products was manually measured, recorded on paper, and then entered into a Quality Management System. Ambient temperature and humidity was impacting the quality and consistency of the product.
Glassdome Solution
The manufacturer deployed Glassdome to conduct real-time product sampling and excursion monitoring. We implemented real-time automatic sharing of measurement data and anomaly detection.
Results
By using food & beverage manufacturing software from Glassdome, the manufacturer saw a 69% reduction in size variability, and a 54% reduction in thickness variability.
Why Glassdome food & beverage manufacturing software?
Of course, we don’t think you should use any old MOMS system. We think you should use Glassdome (especially if you have a batch-based manufacturing process, as we mentioned above). With Glassdome, you get:
Straightforward Deployment
Start strong, refine quickly. Get moving fast with collaborative experts, flexible drag-and-drop software, and out-of-the-box functionality.
More Data from More Machines
See everything all the time. Integrate with older and more complex machines, pull more real-time data points, and maximize downtime reporting.
Results You Can Use
Make your data work for you. Don’t settle for generic data or wait a day for reporting. Start getting better now with food & beverage manufacturing software with helpful reports, seamlessly automated.
Glassdome is clear, simple, and makes your manufacturing operations better.
See for yourself on our site, or get in touch.