Why Does Manufacturing Need to Change?
By Glassdome
It’s the question ringing around factories across the West – does manufacturing need to change? Manufacturers are at an inflection point. Making things and getting them to where they need to be is far more complex than it once was. While manufacturing moves from developed countries to new frontiers, supply chains grow more and more volatile. How can modern manufacturers understand and adapt to these changes?
What’s happening to manufacturing in developed countries?
Since the late-20th century, manufacturing’s share of worldwide value creation has been decreasing. According to the World Bank and OECD, the global share of manufacturing in GDP has decreased from 18.9% in 1997 to 16.6% in 2021 (see chart).
This decline in manufacturing’s importance to the global economy began in leading developed countries. Deindustrialization has been clearly evident in the United States, Europe, and Japan for some time. Recently, it has also been observed in the Four Asian Tigers – South Korea, Singapore, Hong Kong, Taiwan – as well as in China.
In the United States, manufacturing decreased from 16.1% in 1997 to 10.7% of GDP in 2021. In South Korea it decreased from 27.6% in 1988 to 25.5% in 2021. Manufacturing’s share of GDP is falling even in major manufacturing nations like Germany, Japan, and China.
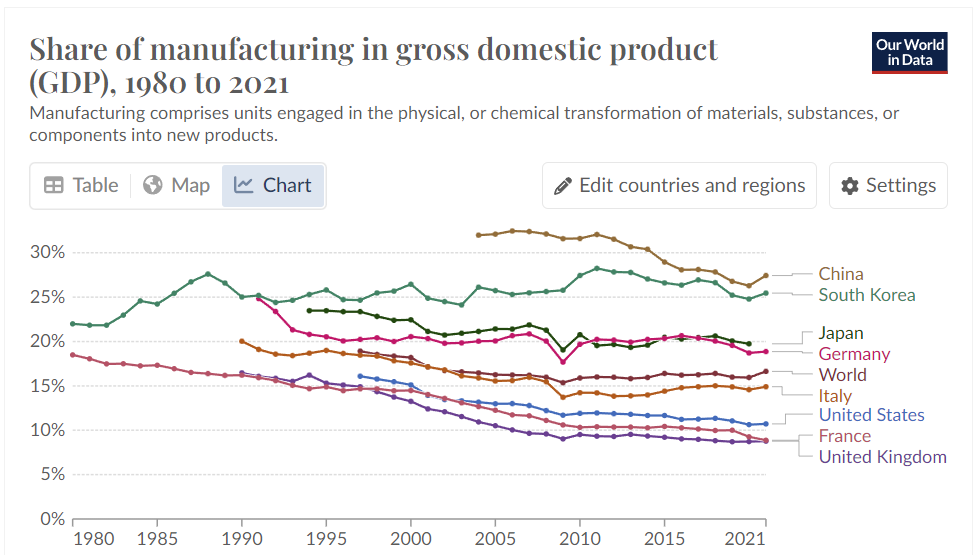
Are developed countries just “hollowing out?”
In addition to deindustrialization, much of this decline in developed countries can be attributed to offshoring, leading to a phenomenon called “hollowing out.” This is when manufacturing facilities move to countries with lower labor costs, resulting in a decline in the manufacturing workforce in the original country. In a social context, it can be dangerous as middle-class jobs disappear, wealth concentration increases among the affluent, and the low-income population grows.
This isn’t a case of self-centered manufacturers looking for marginal gains on their balance sheet. The IMF notes that this decline in the manufacturing share of the overall economy is considered a natural occurrence as the entire economy develops. The fact that consumption expenditures on manufactured goods have remained relatively stable over the past few decades supports this argument.
However, despite these factors, it is undeniable that the traditional manufacturing-centric industrial structure is undergoing a revamp, and manufacturing’s share of the developed world’s economy is decreasing.
Supply chain challenges
The global supply chain has become historically volatile. The Global Supply Chain Pressure Index (GSCPI), which measures the status of the global supply chain by integrating transportation cost data and other manufacturing-related indices, has fluctuated wildly in recent years. This instability is due to trade tensions between the U.S. and China, a worldwide spike in protectionism, and, of course, the COVID-19 pandemic.

Global Supply Chain Pressure Index
How can the manufacturing industry strengthen its competitiveness to overcome these challenges?
Deindustrialization and global supply chain volatility are challenging the manufacturing industry. Without a system that can adapt flexibly to these shifts, the sector may face even greater crises.
That’s why Digital Transformation is the hottest topic in manufacturing innovation.
Digital Transformation (DX) refers to the process of introducing and operating digital technologies to develop new products and innovate existing products or operations. This includes cutting-edge tech like the Internet of Things (IoT), cloud computing, Artificial Intelligence (AI), and big data solutions. Digital Transformation is designed to improve efficiency and customer experiences and create additional value through innovation and new inventions.
The COVID-19 pandemic acted as a catalyst for Digital Transformation. A survey in 2020 showed that 37% of European companies and 27% of U.S. companies had not adopted digital technologies, but in 2021, 55% of European companies felt the need to adopt digital technologies due to the pandemic, and over 46% increased their investments in digital technologies.
Manufacturers have their own subset of DX: Industrial Digital Transformation (iDX). iDX is the process of addressing industrial challenges and creating new value by integrating digital technologies such as cloud computing, big data analysis, AI, and 5G throughout the entire industrial process.
iDX can be broadly organized into four categories: process innovation, product intellectualization, service enhancement, and the creation of new industries and business models.
The future
Despite its promise, Digital Transformation is not progressing as rapidly as expected. While almost all companies have started DX projects in some form or at some level (using tools like the Glassdome Production Monitoring solution), most are struggling to fully complete the initiative and embed Digital Transformation in their DNA.
Companies and governments worldwide are implementing various policies to promote the Digital Transformation of industries. In future insights, we’ll explore the DX promotion policies of different countries and regions.
Looking to implement iDX in your factory to make it more efficient and increase visibility and productivity?
Look no further. Our Manufacturing Operations platform is the best way to cut downtime and raise quality.