Simon Kim: Why I Started Glassdome
By Simon Kim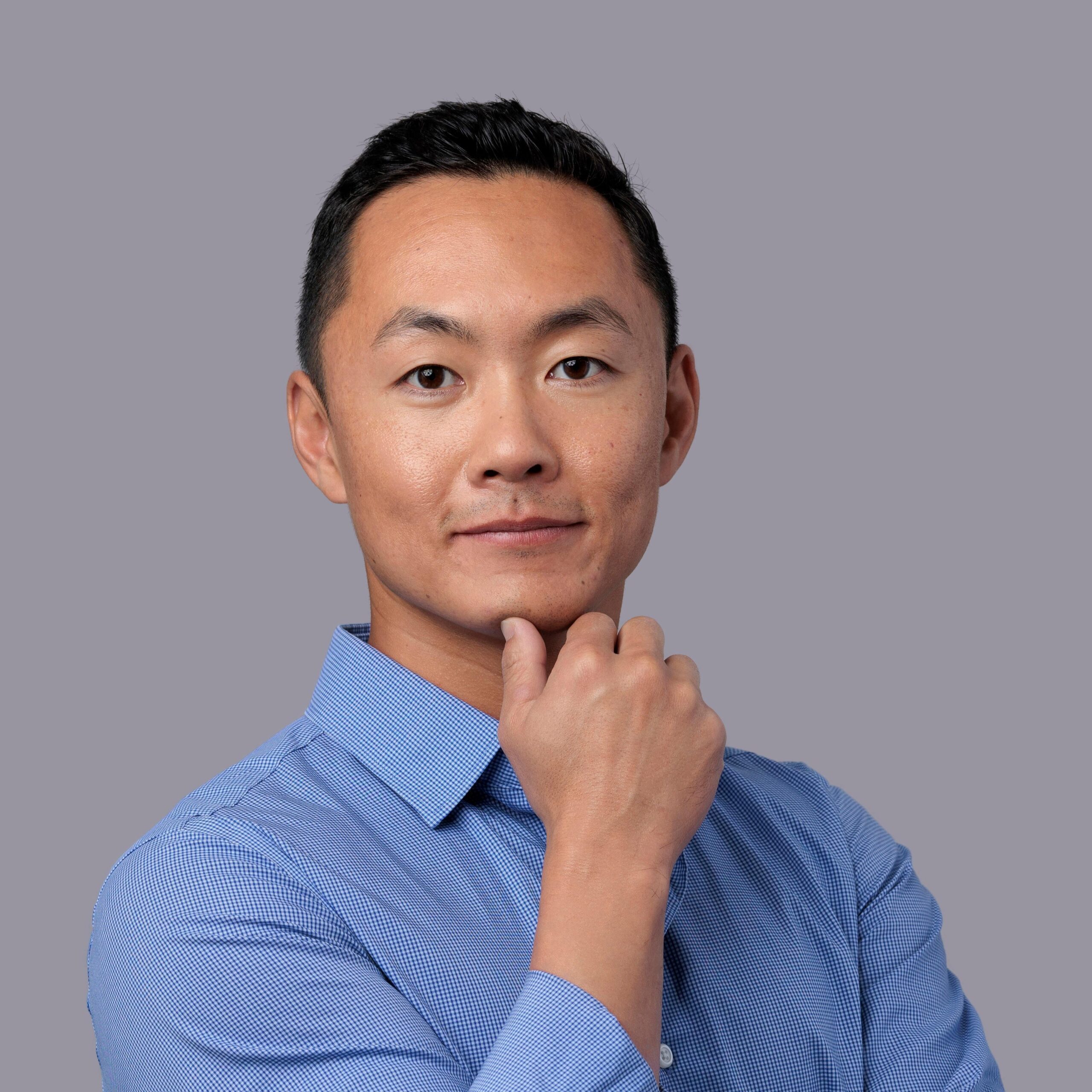
Glassdome began as a fuzzy realization of a vast, important, and underserved market.
As Head of Software and one of the founding team at Awair, I spent five years immersed in IoT solutions for indoor air quality. I saw firsthand how sensor data—like CO₂ and VOC levels—could transform environments from hotels to offices. But by the time I left the company in 2019, I realized that the most powerful potential impact of real-time data had barely been touched. IoT had the power to transform foundational industries with mission-critical use cases.
As a Korean American who grew up in Korea, I always understood that manufacturing plays a major role in the global economy. Yet in the U.S.—where I was educated and spent my adult life—it seemed few recognized its importance; none of my Stanford friends were working in the field. My gut told me that manufacturing was an underserved industry where I could leverage my IoT expertise to make a difference. I incorporated Glassdome to build on that conviction.
Building from one
A few months later, I traveled to Korea at the start of the COVID-19 pandemic. My conversations with local manufacturers kept pointing me to the same glaring issue: High-value machinery was generating tons of operational data, but none of it was standardized or easily accessible. Each machine had a different automation protocol—like all the different printer drivers we used to install—making it nearly impossible to get a clear view of factory performance.
I’ll never forget visiting a corrugated-box plant where a critical production line was down, and the engineers had no idea why. They scrambled between control screens and performed manual checks for hours. It brought home just how much money and time get lost when manufacturers operate blind. Real-time data visibility through direct integration with machines, it turned out, wasn’t a “nice to have.” It was essential for survival. This gave us the conviction to focus on making machine integrations easier and machine data more accessible.
Real-time data visibility through direct integration with machines, it turned out, wasn’t a “nice to have.”
Our first challenge was building software drivers that could speak to a wide variety of factory-floor equipment and their controllers. We needed automation experts who understood industrial protocols, and software engineers who knew modern programming languages, but also knew how to dissect the TCP payloads of Mitsubishi Melsec protocol. It wasn’t easy, especially in the early days when we were five people trying to tackle a massive industry challenge. But we were relentless with our belief that it would benefit the industry.
Solving mission-critical challenges
Luckily the work began to pay off. One of our earliest big wins was with a major baked-goods producer in Korea. They wanted to track quality across billions of products, from dough prep to packaging. The factory lines consisted of tens of different machines from a variety of vendors all with different controllers.
Our IoT devices and software, though initially bare-bones, collected and centralized these machine data directly from their cabinets with minimal infrastructure overhead. This let their factory operators spot quality issues early, rather than waiting for recalls and rework. That was a turning point—seeing how direct, real-time data from machines could shift an entire production process from reactive to proactive and save lots of money and time for our customer.
Another inflection point happened in 2022, when we learned that a global battery maker needed to comply with new EU regulations such as the EU Battery Regulation and CBAM. These regulations required real, site-level data—no assumptions or average estimates. Our platform was already extracting real-time data from factory floors, so we saw an opening to expand into carbon tracking.
Although it was an entirely new field for us, we invested heavily to bring on Life Cycle Assessment specialists and secured ISO 14067 verification for our entire solution—becoming the first product carbon footprint platform to do so. We are very proud to say that our customers can now measure and report actual emissions, not vague estimates, right from the machines that made their products.
Today, we help manufacturers—from forklift makers to defense component producers—gain complete visibility across their machines and processes. Manufacturers, especially small-to-medium-sized companies, shouldn’t have to spend a fortune to access real-time data from every piece of equipment. With our native drivers and field-level support, we deliver extensive yet affordable machine integration—with no excuses like “that machine is too old” or “too unique.” After all, these machines produce the products, and without tight control over their performance, a manufacturing operation can’t run effectively.
Believing in the future of manufacturing
I believe that a manufacturing organization’s operational excellence and sustainability both depend on one element: high-quality, real-time data. At Glassdome, our commitment to serving manufacturers by leveraging real-time machine data enables us to offer a production monitoring system and product carbon footprint solution that are cost-effective and of the highest fidelity. With a solid data system in place, manufacturers can simultaneously meet sustainability requirements and address operational efficiency.
Our mission is to empower manufacturing companies to create an abundant and sustainable future—a responsibility we take seriously because manufacturing underpins modern life.
With the US trade deficit on the rise, and the threat of tariffs on the horizon, producing goods domestically is more important than ever. A thriving manufacturing sector means more high-paying, quality jobs and a stronger economy. We’re proud to do our part by making machine data more accessible and affordable for as many manufacturers as possible. It’s still early days for us at Glassdome, and we’re excited to see how much more we can contribute to the manufacturing industry.
Want to learn more about how we help manufacturers thrive?
Handle your mission-critical operations and sustainability challenges with Glassdome