Manufacturing Downtime Challenges and Solutions
By John Wright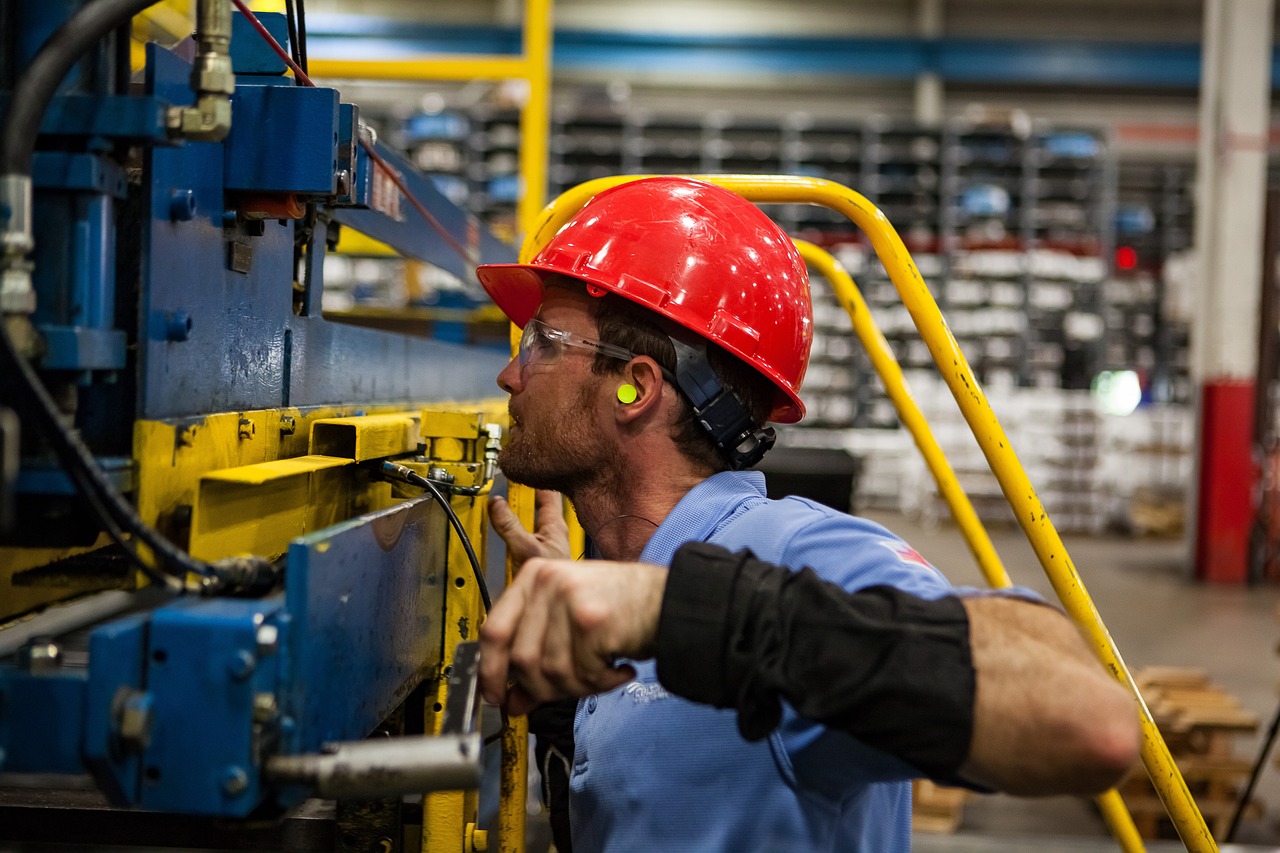
Manufacturing downtime refers to any period of time when production is stopped, whether planned or unplanned. It’s a silent killer for any factory. Every minute a machine or line is down means lost OEE, productivity, and profitability.
Cutting downtime directly correlates to corporate success. In this insight, we’ll go over the key impacts of manufacturing downtime, common root causes, and how you can mitigate its effects and even solve it in your facility.
Impacts of manufacturing downtime
Downtime leads to negative impacts across your operations.
Financial losses: Idle equipment and halted production mean lost revenue, while repairs, overtime, and missed deadlines actively cost money.
Lower productivity: Workers are idled or reassigned to less productive tasks, affecting productivity per employee and reducing morale.
Equipment wear and tear: Stoppages and restarts can accelerate machinery degradation, causing more frequent breakdowns and higher maintenance costs.
Supply chain disruption: Downtime in one link can cause effects up and down the supply chain as raw materials delivery delays, inventory shortages, and missed deadlines ripple outward.
Compliance and safety risk: Prolonged or frequent downtime can cause facilities to fall out of compliance with industry regulations and safety standards, exposing companies to legal or financial penalties.
Over time, these issues can compound, leading to delayed deliveries and a decline in customer satisfaction and loyalty that threaten your firm’s reputation and viability.
What causes manufacturing downtime?
Every downtime instance is unique, but most of them fall under one of five overarching categories:
Equipment failure: Regular wear and tear or surprise breakdowns can both cause machines to stop and lines to go down.
Human error: Mistakes, improper handling, and poor training can all cause downtime. As much of America’s skilled industrial workforce gets older and retires, taking their knowledge with them, this issue grows larger by the day.
Technical failures: Outdated or poorly integrated software systems can mean production scheduling, inventory management, and machine operations aren’t well-optimized, and in worst-case scenarios cause them to go completely haywire.
Material shortages: If you don’t have the ingredients, you can’t bake a pie. Delivery delays and inventory mismanagement can stop a factory dead in its tracks.
External factors: “Acts of God” in insurance parlance. Natural disasters, power outages, political upheaval, or pandemics can all cause manufacturing downtime on top of their other impacts.
What are five ways I can reduce manufacturing downtime?
Predictive maintenance: Using IoT sensors and analytics to identify issues before they cause downtime can dramatically reduce machine failure rates. It also reduces the need for planned downtime for regular inspections.
Training and workforce development: Regular training equips employees with necessary knowledge and skills to handle machinery properly, use technology tools effectively, and respond to emergencies. Maintaining an employee knowledge base online will help mitigate the impact of veteran employees leaving the company.
Redundancy and Backup Systems: It can be expensive, but backup or duplicate machinery reduces the impact of any single piece of equipment failing.
Supply Chain Management: Using digital tools to optimize inventory and maintain strong supplier relationships helps reduce material shortages that cripple production lines.
Continuous Improvement programs: Adopting lean manufacturing, continuous improvement, and / or Six Sigma principles like the 4M Method helps managers and employees spot inefficiencies and cut downtime.
What should I do next?
Trying to start all of this on your own is a daunting task. Glassdome’s Production Monitoring solution can help with real-time visibility using real data.
Glassdome pulls data from your existing hardware, along with IoT sensors we install on your factory floor. Our customizable displays then show you exactly how each aspect of your production process is doing at any given time. And installation is relatively simple, with little reliance on external software outside of your machine drivers, and built-in connectivity.
Ready to use your data to start cutting downtime?
Talk to a Glassdome manufacturing expert today.