How Continuous Improvement Helps Manufacturers Solve Staffing Challenges
By Max Krevitz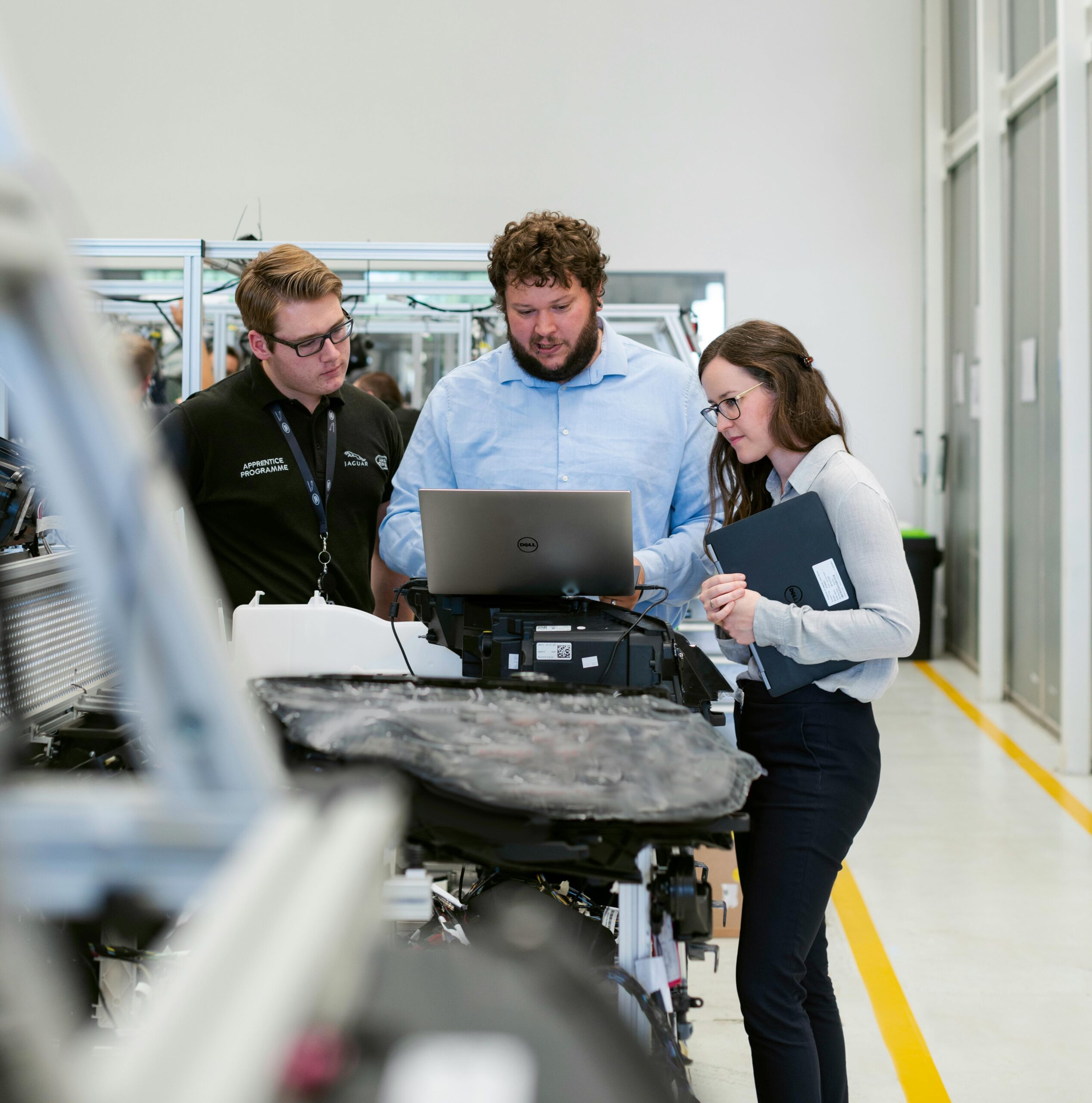
America is facing a labor crisis, with an imminent shortage of up to 6 million workers, and need tools like Continuous Improvement to solve the staffing challenge. Manufacturing is particularly hard-hit.
The skilled industrial workforce is getting older. Younger generations are pursuing careers in service industries. Immigrants can backfill that gap to some degree, but require careful, time-intensive training. And once a worker is trained, they’re immediately vulnerable to being poached by a competitor.
Smart manufacturers are adapting. One of the best ways to alleviate staffing issues is to adopt Continuous Improvement (CI) processes and technology.
CI helps build factories with better visibility, culture, and process. All of which help you get the most out of the employees you have, and train the new ones that come in.
Better visibility
Continuous Improvement starts with being able to see what’s happening on your factory floor (That’s why Glassdome offers real-time visibility in our platform). Seeing a problem is the first step to fixing it.
One client example is in a confectionary factory. Our client’s quality control process involved a person responsible for randomly selecting chocolate cakes, measuring their dimensions with calipers, writing them down on a clipboard, and reporting the numbers back.
This employee didn’t directly contribute to increasing production, and if there was an out-of-tolerance cake, it would take hours (and hundreds of potentially poor quality cakes rolling through the line) before it was noticed and the fault was fixed.
Glassdome worked with the client to replace the calipers and clipboard with an automated system. Quality metrics improved, and the worker was assigned to a line that needed more manpower, solving two issues in one fix.
Another benefit of process visibility is enabling smart preventative maintenance. You can keep your process humming with a leaner staff with the ability to see small shifts in machine performance and codifying maintenance schedules and results.
Fixing broken machines and dealing with fire drills takes more staff, on uneven hours, and adds hours and hours of downtime. Who needs that headache?
Process insight
CI demands a good map of your process, much the same way it works better with real-time machine and quality visibility.
Visualizing and managing your processes helps you perfect your workflow, minimizing downtime and movement around the factory, and making sure the staff you have are directly impacting production at all times, instead of moving things around or waiting for other workers to finish their components.
Related methodologies like lean manufacturing and Kanban can help a lot in this effort.
Documenting and codifying processes also makes training a new employee easier. You can even use your data to bolster their training with AI.
It also means that one knowledgeable person leaving is less likely to cripple a department or process. Their knowledge is written down and ready for the next person to pick up and use.
Collaborative culture
CI is at its core a focus on incremental updates. Each day, every process can get optimized and streamlined. Instead of your staff waiting around for the next top-down revolution, they’re incentivized to find small ways to enhance their performance.
The emphasis on bottom-up improvement isn’t just about the day-to-day upgrades (although they certainly help).
Feeling valuable and heard keeps staff motivated and engaged, reducing turnover. Delivering real, positive results, and being appropriately noticed and rewarded, fosters positive encouragement and open communication.
What next?
Our Production Monitoring platform has the real-time data visibility and customizable dashboards and reporting you’ll need to implement a durable, useful CI program. (And you can use it in combination with our Product Carbon Footprint solution to get greener while you get more efficient).
Staffing issues starting to bite hard? Or just trying to future-proof your factory? Glassdome can help.
Get in touch today to learn more.