Why Operational Efficiency and Sustainability Aren’t Competing Interests
By John Wright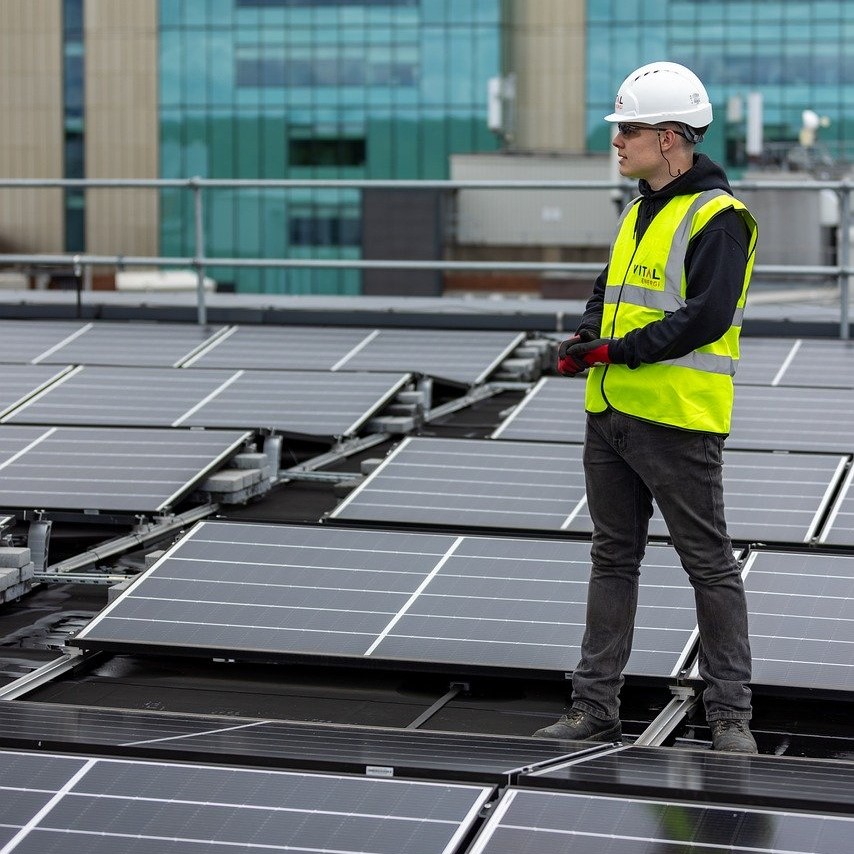
Making more money and making the world a better place are often framed as a tradeoff – operational efficiency battling with sustainability investment.
But a better way to think about it is that production issues and carbon emissions are just different ways to measure inefficiency. When you work towards solving one metric, the other usually improves.
That’s why we offer Production Monitoring and Product Carbon Footprint (PCF) solutions. Because they naturally work in sync.
Better performance uses less energy
Put simply, better performance leads to less waste. Less waste means each finished product takes less energy to produce.
Our Production Monitoring software is usually used to improve three key metrics: better quality, less downtime, and faster problem solving.
Improved quality means less out-of-tolerance product is produced. When an out-of-tolerance end product is thrown out, the carbon price of its inputs is spread out through your good products, increasing their carbon footprint. When more of your inputs are going into products you can actually sell, the lower each of their individual PCFs will be.
Less downtime means your factory runs more efficiently. All that time your line is down, you’re still keeping the lights on and running other machines. Energy is a major component of a PCF. When your line runs efficiently, your energy input per product drops.
Faster problem solving can affect your PCF in a few ways. A shorter feedback loop means an issue on a line can be fixed before it has cranked out hundreds of poor quality products. Visibility into temperature fluctuations means you can quickly mend a loose oven cover – improving quality and reducing wasted energy. Shift-to-shift variation can be identified and rectified, with similarly green results.
This all also works in reverse. Each of these examples could be a key recommendation that emerges from a Product Carbon Footprint consulting engagement.
Same datasets, different calculations
The beautiful thing about the overlap between operational efficiency and sustainability is that they use very similar datasets.
Throughput, availability, and quality are the cornerstones of Overall Equipment Effectiveness (OEE), and they all impact the energy used to make a product.
PCF’s laser focus on the inputs you use to make your product can be used as a forcing mechanism to find ways to decrease their amount and their cost.
Once you have a functioning data pipeline from your factory floor to your manufacturing operations platform, the possibilities for what you can improve begin to look endless.
What’s this mean for me?
You can use sustainability goals to drive operational efficiency. Or vice versa.
And the overlap in datasets means if you have one data acquisition solution that can do both kinds of calculations, you’re in great shape.
Most customers come to us with a pressing need for either an operational or sustainability solution. But the symbiotic relationship between the two means it’s easy to apply the other solution to the same factory or product.
So why not handle both at the same time?
Get carbon compliant and a lot more efficient, all at the same time. Set up a time to chat with one of our experts and we can see if it can work for your unique process.