MES or QMS or Production Monitoring – Which is Right for My Business?
By Max Krevitz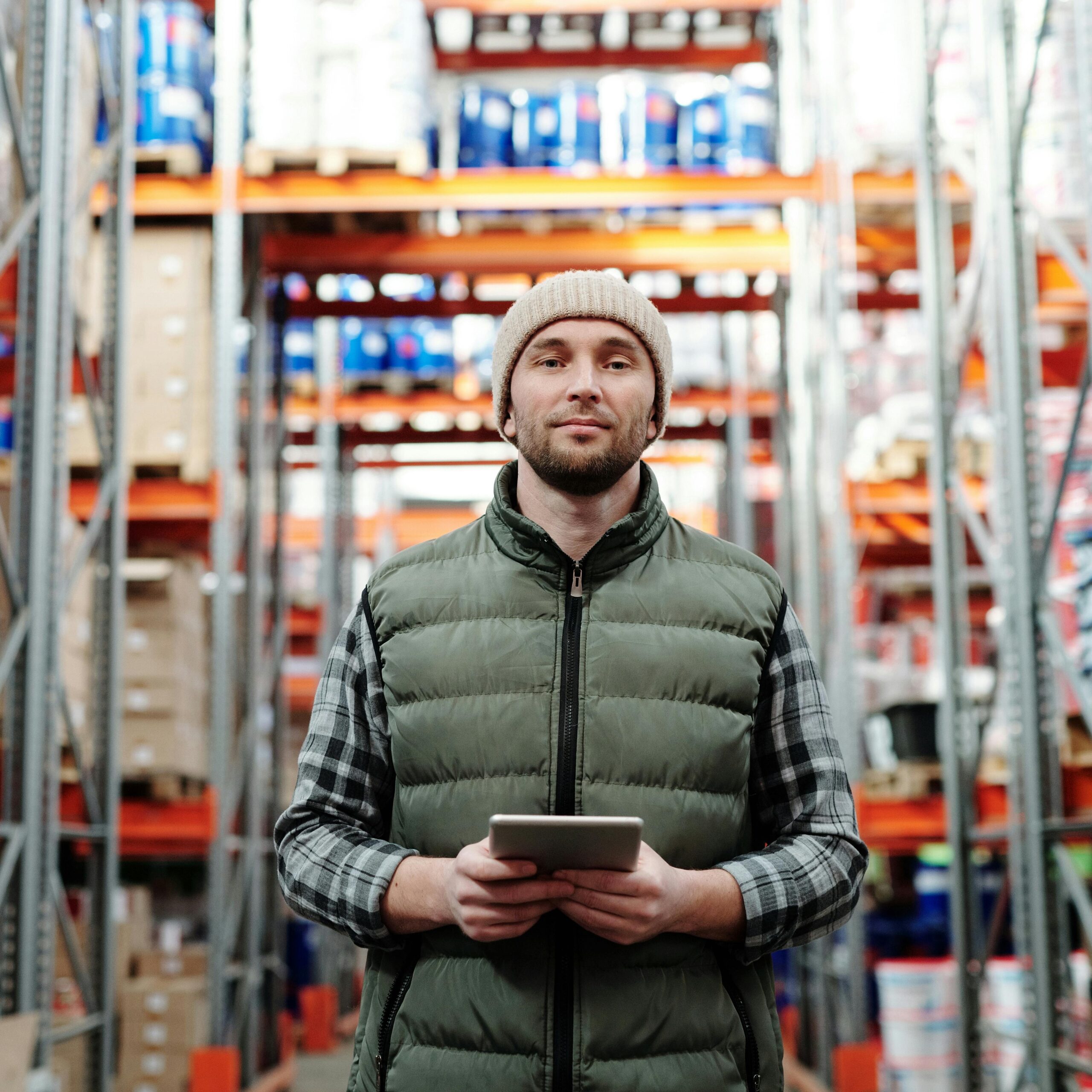
When you’re a small-to-medium sized manufacturer, there comes a time when you realize that creating your product the old fashioned way just isn’t cutting it. You need technological help. That moment could be instigated by growth, experienced staff aging and leaving, or implementing lean manufacturing or continuous improvement programs. Most manufacturers zero in on two acronyms: an MES or QMS software. We’ll also offer a third up for consideration: Production Monitoring software.
MES: Manufacturing Execution System
QMS Software: Quality Management System software
What do each of these things do? When are they the right (and wrong) tool for the job? And which is right for my company?
MES: Manufacturing Execution System
What is an MES?
An MES is a piece of software that monitors and controls production on a manufacturing floor. The MES sits in between planning and control systems like an ERP (enterprise resource planning) system and the actual manufacturing operations.
An MES is a powerful, wide-ranging tool that can handle functions including:
- Resource allocation and status
- Management of:
- Labor
- Quality
- Process
- Maintenance
- Scheduling
- Production dispatch management
- Document control
- Product tracking
- Performance analysis
In short, it monitors, tracks, documents, and controls the process from raw materials to finished goods.
Note: Glassdome integrates with many MES systems, including SAP, Rockwell, and Siemens.
What are the benefits to deploying an MES?
A fully deployed and integrated MES tracks and visualizes an enormous amount of data and can enhance productivity and ultimately profitability. It also helps with compliance in regulated industries.
Common benefits to deploying an MES include:
- Reduced human error
- Better quality control
- Lower downtime
- Less inventory (and related storage costs)
- Consistent product genealogy
When isn’t an MES the right choice?
While an MES is a powerful tool, it has its downsides, most of which relate to its size and complexity.
MES software is a huge upfront and ongoing investment of time and money. They cost a lot, implementing them is complex (and that complexity increases exponentially if software besides the ERP system needs to be integrated), and the entire company needs to be brought onboard with change management.
Deploying an MES is a great idea for large companies with cash on hand, dedicated IT resources, and large operations staff. It can be a bridge too far for many small-to-medium sized companies.
QMS (Quality Management System) Software
What is QMS software?
Let’s start with the acronym alone.
A quality management system is a codified set of policies, processes, and responsibilities that keep your business (and factory floor) running smoothly. In a manufacturing environment, a QMS is more tightly defined around making sure that the factory is producing 100% good parts (a key component of OEE).
QMS software is a platform that helps digitize, organize, and streamline your QMS.
It can be used for:
- Project planning
- Audits
- Supplier quality control
- Issue management & problem solving
- Change management
- Compliance reporting
A QMS software deployment should essentially take your whole set of operational policies, processes, and responsibilities and put them in the cloud (or a server).
What are the benefits to deploying QMS software?
The ultimate benefit of QMS software is higher quality products and less waste. It can also be a powerful tool for compliance and regulatory requirements.
It accomplishes this through:
- Codifying and digitizing a quality-first culture
- Visualizing quality metrics
- Recognizing potential problems before they occur
- Tracking production and troubleshooting issues
When isn’t QMS software the right choice?
As the name suggests, QMS software is a narrow solution. It’s more of a component of continuous improvement efforts across the manufacturing process than a holistic solution.
An MES or CI solution might actually include many of the quality management tools a QMS system provides.
Production Monitoring Software
What is Production Monitoring?
Production monitoring makes continuous improvement work. Continuous improvement is a process of improving products, services, and processes through incremental, often bottom-up, changes. Instead of waiting for revolutionary change, it emphasizes the power of consistent upgrades. First implemented on a large scale at Toyota, it’s a cornerstone of methods like Six Sigma, lean manufacturing, and total quality management.
It’s usually implemented according to the plan-do-check-act cycle:
- Plan: Identify an opportunity and plan for change.
- Do: Implement the change on a small scale.
- Check: Use data to analyze the results of the change and determine whether it made a difference.
- Act: If the change was successful, implement it on a wider scale and continuously assess your results. If the change did not work, begin the cycle again.
Production monitoring software empowers that cycle. Process visualization through custom dashboards means operators and managers can see where they need to change, and measure the impacts of their work. Integrated checklists and instructions ensure knowledge is shared widely and quickly.
Put simply, users can:
- Monitor and analyze production in real time
- Identify areas for improvement
- Track labor efficiency for optimal staffing
- Automate asset and production reports
What are the benefits to deploying production monitoring software?
Production monitoring software can enhance employee engagement, measure and systematize processes, and improve quality. With it, an ERP system, frontline workers, machines, and operations software can be brought together in one pane of glass.
Metrics that can be measured and improved include:
- Downtime
- Quality
- Waste
- Efficiency
- OEE
- OLE
- PCF
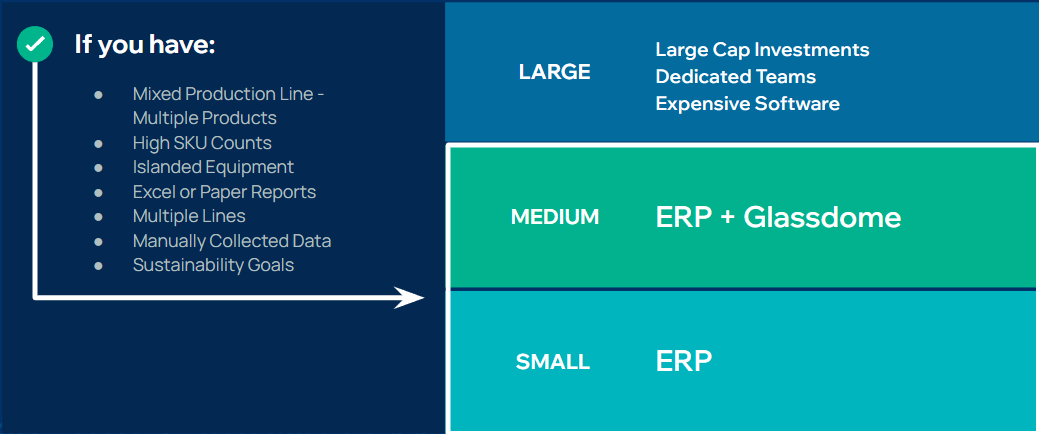
For manufacturers with mixed-model production, high SKU counts, and expensive per-product outputs, it’s an especially great tool.
When isn’t production monitoring software the right choice?
A production monitoring tool isn’t for every manufacturer. Sometimes an MES or QMS is the right tool for the job.
If your company has a huge footprint and a lot of spare cash, you’re probably looking for an MES. It’s a more comprehensive solution.
If you have an assembly line that makes a whole lot of the exact same thing with tight margins, you might not reap as many benefits as mixed-model manufacturers (although visibility will still net you improvements in quality and problem-solving speed).
Still looking for production monitoring software?
Decided to look beyond MES or QMS? You’re in the right place – We’re trusted by some of the largest manufacturers in the world.
The Glassdome Production Monitoring platform uses real data from proprietary sensors and gateways to show a real-time view of your shop floor. Our consultants are manufacturing veterans, who ensure your data pipeline and dashboards are tailored to your needs.
Our ISO 14067 verified Product Carbon Footprint solution uses the same data to handle environmental compliance reporting for even broader functionality.
Start cutting downtime and getting more efficient today
Get in touch with a Glassdome manufacturing expert