How can U.S. manufacturing attract younger generations?
By Glassdome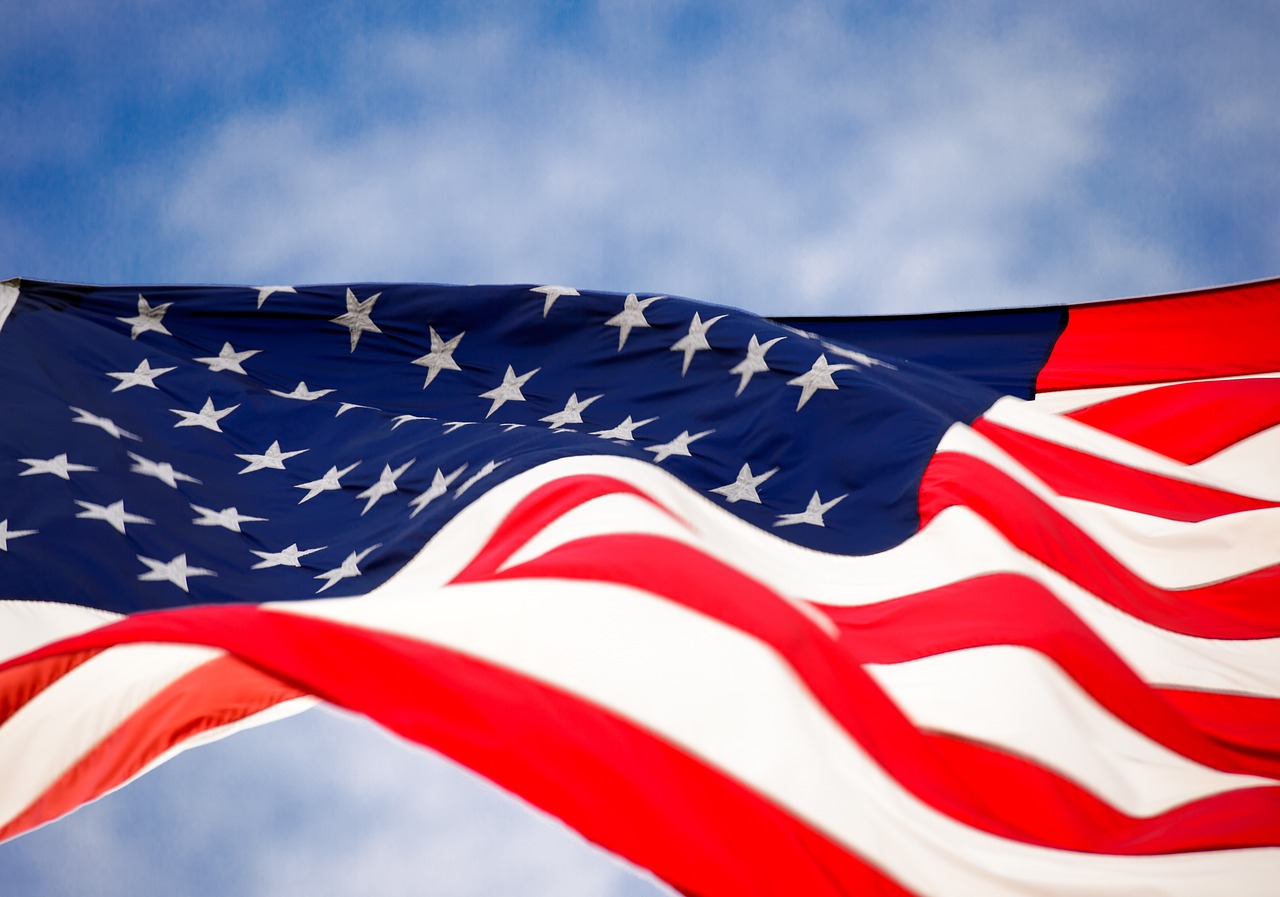
The U.S. manufacturing industry is grappling with a significant labor shortage, exacerbated by an aging workforce and a struggle to attract younger generations. As older workers retire, there’s a pressing need for a new, younger workforce. However, the industry is having a challenging time attracting millennial and Generation Z workers.
Showcase modern manufacturing
One major reason for younger generations’ reluctance to start a career in manufacturing is a negative perception of what it’s like to work in the industry. Despite advancements in automation and technology at manufacturing sites, many young people still view the sector as physically strenuous, hazardous, monotonous, and outdated.
Millennials and Generation Z seek meaningful work and are digitally savvy. To attract them, it’s crucial to highlight the industry’s embrace of cutting-edge IT technology and its shift away from repetitive manual tasks.
Showcasing real-life examples of young workers applying digital technology in manufacturing, emphasizing how they’re managing processes and adding value, could be persuasive. Effectively using popular social media platforms like TikTok and Instagram could effectively communicate these changes.
Take training to the 21st century
Secondly, the limited availability of educational opportunities within the industry poses another barrier. It’s hard to get up to speed on a factory floor. Most of the key knowledge is locked away in the heads of older technicians. Given that 84% of manufacturers as of 2021 were small and medium-sized businesses, resource constraints may contribute to this issue.
Introducing mentorship programs where experienced workers train newcomers, or implementing e-learning programs, could help bridge this gap. Digitizing training materials and leveraging video tutorials or digital documents would resonate well with the tech-savvy younger generation. As companies progress in digital transformation, these initiatives also offer an opportunity for young workers to acquire IT skills.
Find a flexible work-life balance
Third, young workers see manufacturing work environments as rigid, even as many other industries embrace remote work. Since the COVID-19 pandemic, young workers are demanding work flexibility. But that’s hard to achieve when workers need to be on the factory floor to run machines and oversee processes.
The chart below illustrates how companies have addressed the demands for workplace flexibility among their employees, according to the survey conducted by National Association of Manufacturers.

(Source: https://nam.org/wp-content/uploads/2023/03/Manufacturers_Outlook_Survey_March_2023.pdf )
Addressing this in manufacturing requires maintaining production continuity and enabling remote process management – both achievable through comprehensive digital transformation.
Effective management can be achieved even without constant on-site presence by implementing automation across all processes and enabling real-time monitoring. Analyzing the data gathered from these processes can uncover new insights, leading to more streamlined management. This approach not only enhances productivity but also allows employees more flexibility to choose their work hours.
When this process management system operates on cloud technology, it enables employees to perform many of their duties beyond the confines of the factory. That enable the hybrid work flexibility younger employees crave.
Building a modern workforce
Digital transformation tools like the Glassdome Production Monitoring platform bring an obvious boost to productivity. And gaining a comprehensive understanding of the manufacturing process and fostering a culture that embraces technology can be instrumental in helping manufacturing attract younger generations This modern approach aligns with the expectations and skill sets of the newer workforce, making the manufacturing industry a more attractive career choice for them.
Where should you start your digital transformation? Talk to us about it.
Our manufacturing operations experts are industry veterans. And our manufacturing operations platform can help you get more efficient, compliant, and flexible