Improved quality and efficiency for a food manufacturer
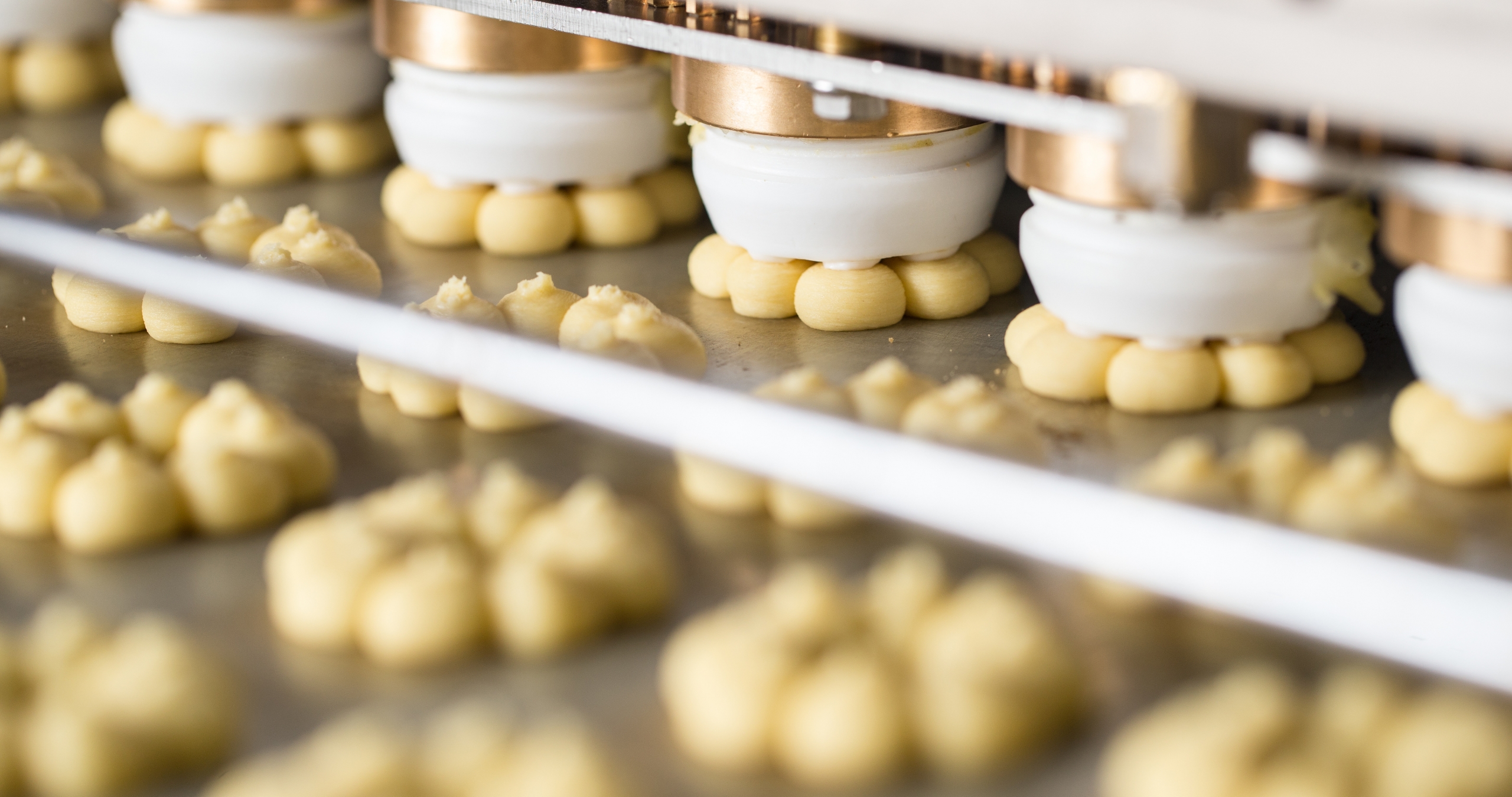
CHALLENGES
- Measuring and entering product quality data by hand into the system
- Identifying causes of product quality decline took weeks or months
- Increasing TCO (Total Cost of Ownership) of their operating quality management system

SOLUTIONS
- Real-time data collection and quality monitoring through wireless gateways
- Easy no-code data integration management linked to existing systems like ERP and MES
- Quality predictive values delivered through insightful data analysis
RESULTS
Percent of data automatically collected:
BEFORE GLASSDOME
33%
AFTER GLASSDOME
100%
Equipment anomaly detection time
BEFORE GLASSDOME
MINUTES TO HOURS
AFTER GLASSDOME
WITHIN A FEW SECONDS
Time to identify cause of quality decline
BEFORE GLASSDOME
WEEKS TO MONTHS
AFTER GLASSDOME
WITHIN A FEW HOURS
Standard deviation of product size / thickness
BEFORE GLASSDOME
0.49/.031
AFTER GLASSDOME
0.15/0.11
POWER UP YOUR
MANUFACTURING EFFICIENCY AND CARBON REPORTING
