See how Lotte Wellfood used Glassdome and AI to improve quality and efficiency
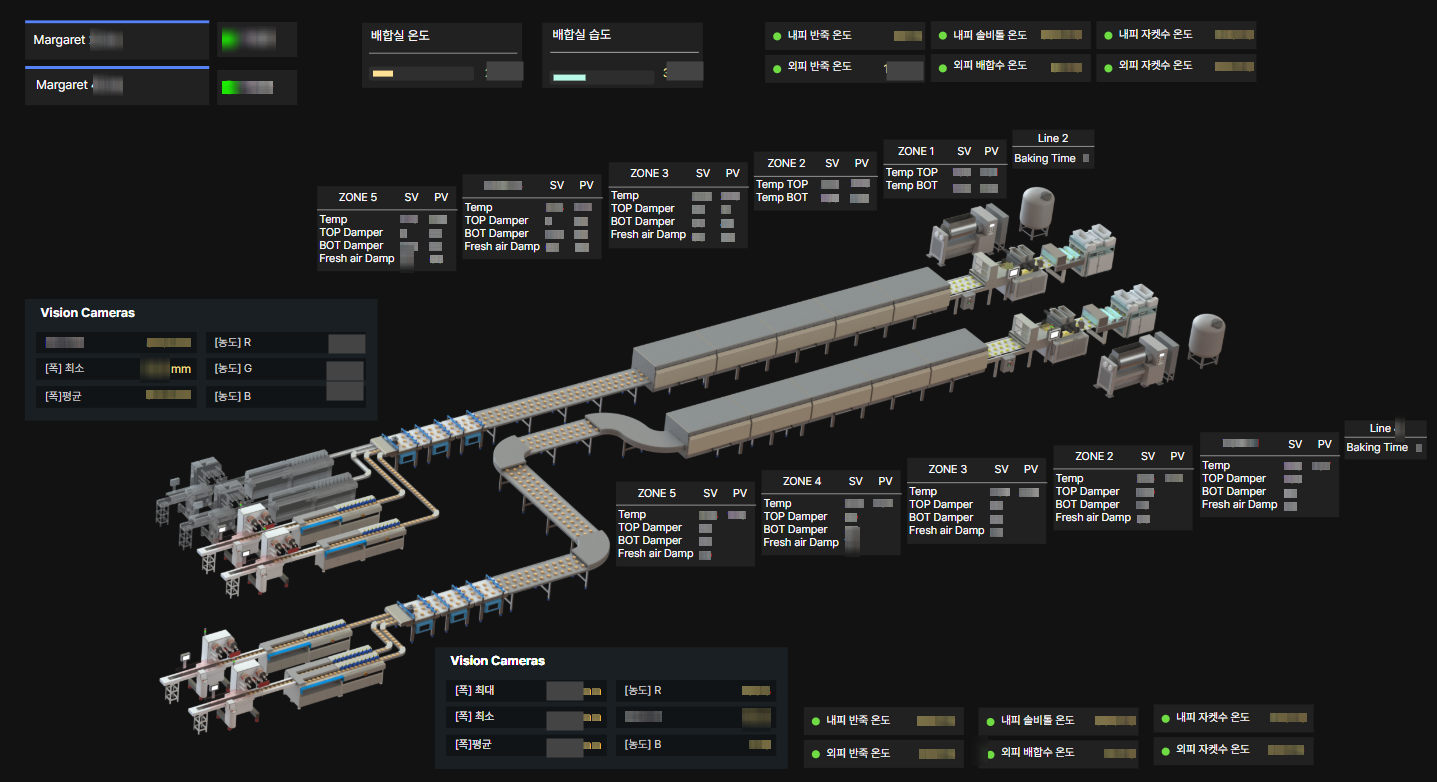
OVERVIEW
Lotte Wellfood is a $3.3b food company and the pioneering producer of snacks like the original Choco Pie dessert and snack cake and Margaret brand peanut cookies.
CHALLENGES
Lotte Wellfood wanted to solve issues with product quality while maintaining and ultimately improving production efficiency across multiple lines and facilities. And they wanted to do it all with a single platform.
To solve both challenges, that solution was going to need:
- Real-time visibility into manufacturing data
- Correlation between production variables and final product quality
- Automated, data-driven quality control processes
- Predictive analytics and data-driven process optimization
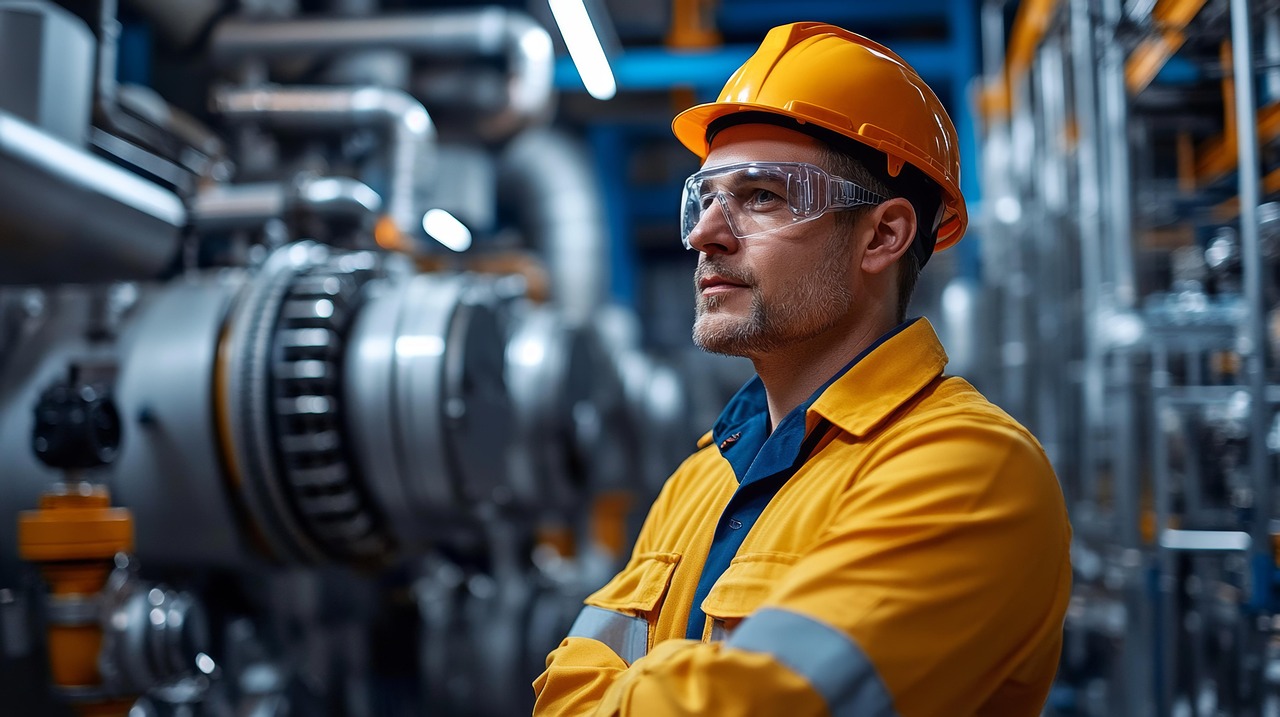
SOLUTIONS
We installed our real-time, data-driven Production Monitoring solution across the factory.
We deployed an automated data flow with sensors installed at key points in the production process, including mixing, kneading, baking, and packaging.
Our IoT hardware allows us to measure various factors such as mixing conditions, oven temperature, and product size.
Real-time production visibility: Centralized monitoring of both production lines through a unified interface.
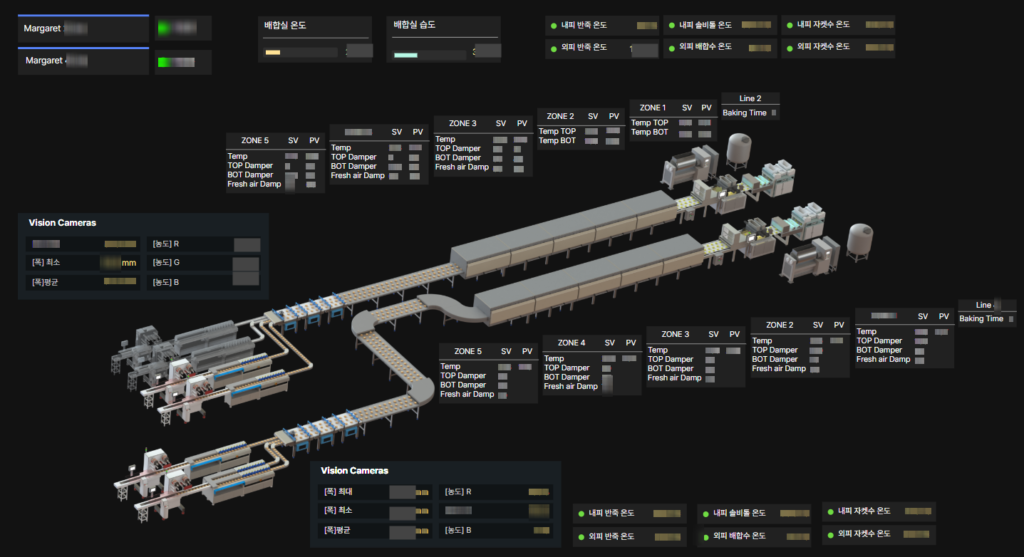
Centralized data storage: A single source of truth enabling uniform data access and seamless collaboration across the plant.
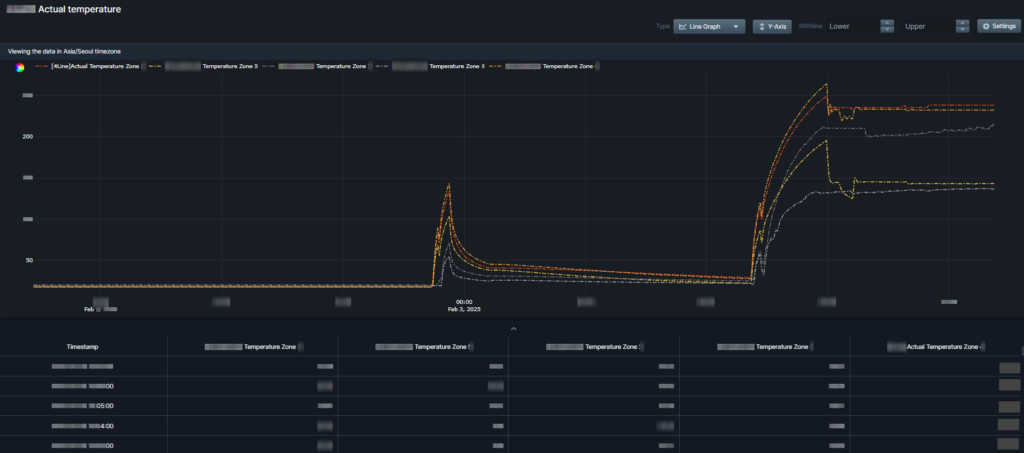
Advanced quality control: We developed and installed a real-time quality inspection system with 3D cameras across the plant
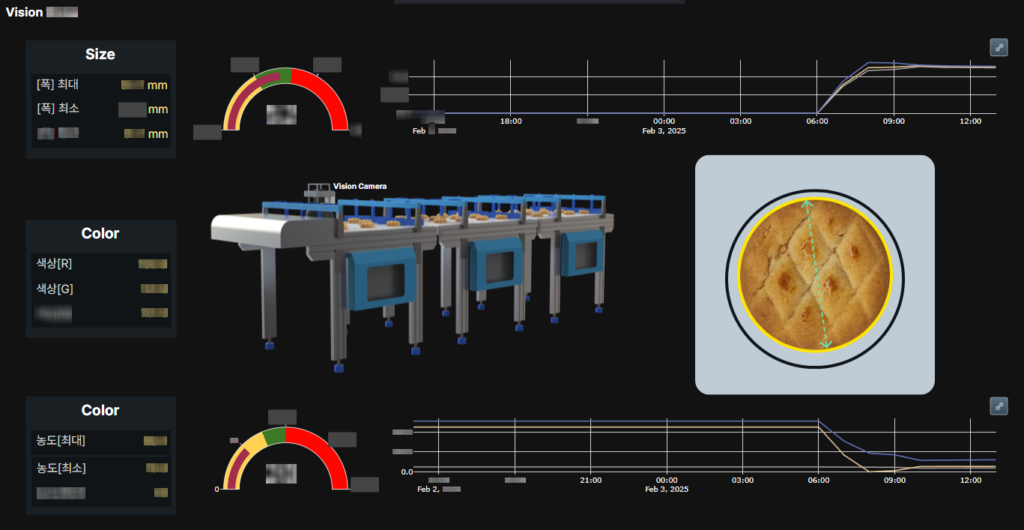
Hardware integration: We installed IoT equipment including gateways, PLC modules, smart sensors, cameras, temperature and humidity sensors, and Ethernet hubs to create a comprehensive data pipeline.
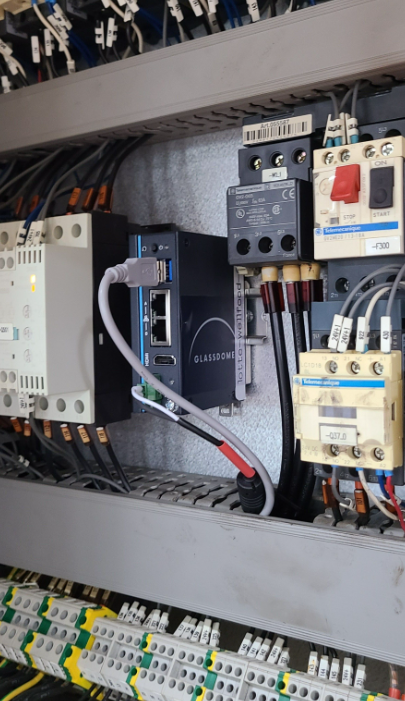
AI-Powered data analysis and optimization: We collaborated with SK C&C to develop and implement an AI Quality Prediction Model, which we installed on the line that produces Margaret brand peanut cookies.
Advanced machine learning algorithms, such as LightGBM and AI-driven simulations, were deployed to forecast optimal production conditions and ensure precise product output.
Based on the model’s analysis, Lotte Wellfood adjusted key variables such as mixing conditions, oven temperature, and other critical factors to create consistent cookies.
RESULTS
Lotte Wellfood saw immediate benefits across their facility, from instant responses to downtime issues and production bottlenecks, to far more informed decision making
Responses to production line issues
BEFORE GLASSDOME
Long stoppages and manual searches
AFTER GLASSDOME
30% faster response time
Quality control process
BEFORE GLASSDOME
Multiple workers assigned to quality control
AFTER GLASSDOME
Automated processes and higher quality
Energy costs
BEFORE GLASSDOME
High and growing
AFTER GLASSDOME
Lower and consistently monitored
Consistency between shifts, lines, and facilities
BEFORE GLASSDOME
Uneven and hard to measure
AFTER GLASSDOME
Uniform quality across Glassdome deployments
Lotte Wellfood is expanding the Glassdome solution to five additional production lines in 2025.
“Previously we were used to seeing very inflexible software vendors quote us millions of dollars for a fraction of features that Glassdome provides. We were really impressed with Glassdome’s field service for setting up new sensors and devices, and now are able to gather real time data for our major lines and use them in a browser. We’re very happy with Glassdome!”
POWER UP YOUR
MANUFACTURING EFFICIENCY AND CARBON REPORTING
