See how a forklift manufacturer uses Glassdome to boost efficiency
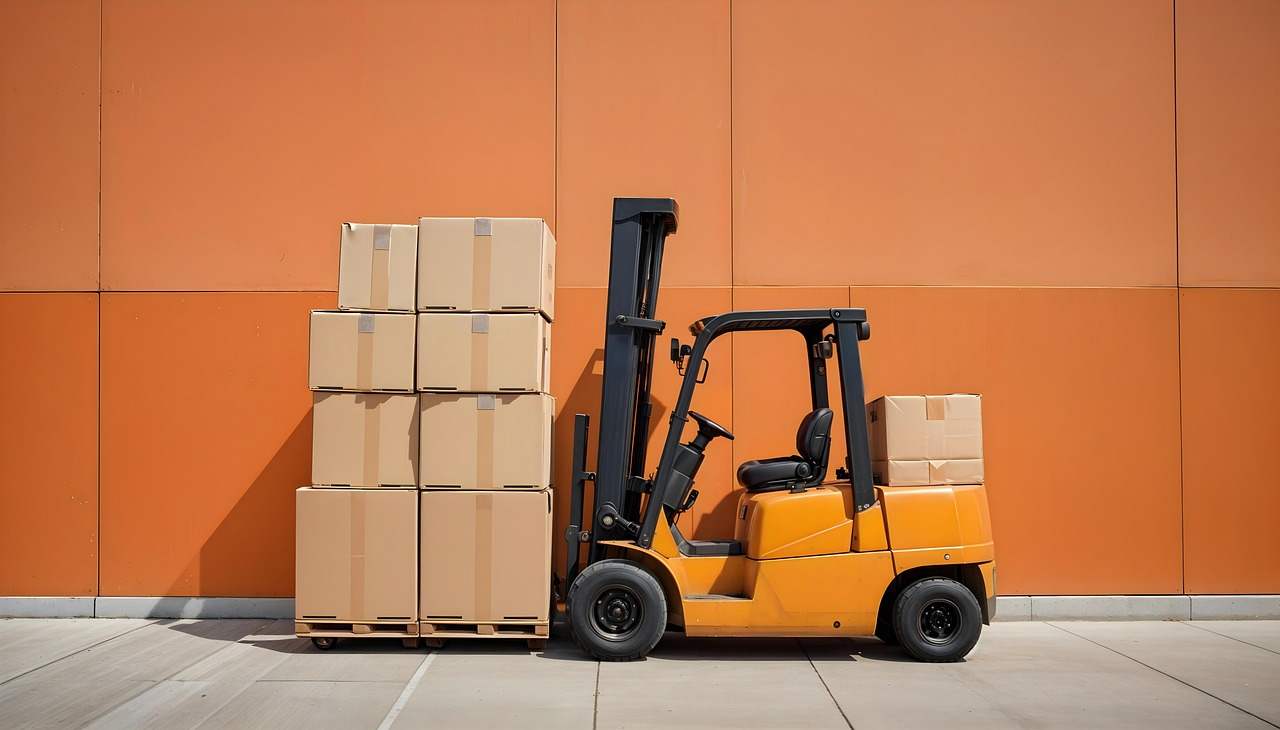
OVERVIEW
Our client is one of the largest forklift manufacturers in the world, with over $660mm in revenue in the Americas.
CHALLENGES
The client wanted a unified view of their Texas factory to increase efficiency and cut down on bottlenecks. But they ran into two common issues.
First, most modern machine OEMs have their own cloud monitoring platform. This is great if you have the same brand across a facility, but that is very rare. Most manufacturers end up needing to subscribe to a variety of OEM cloud platforms.
Second, while retransmitting data collected from a machine to the cloud is common, there is usually no context for that data. Analyzing the data puts the burden of administrative work and calculation on an overstretched operations manager.
Our initial project involved three locations within the plant, Special Products, Main Line 1, and the Paint Room. Each room contained multiple types of machines with varied levels of digitization and internet access. They included machines from Haas, Hornet, and Koike Aronson.
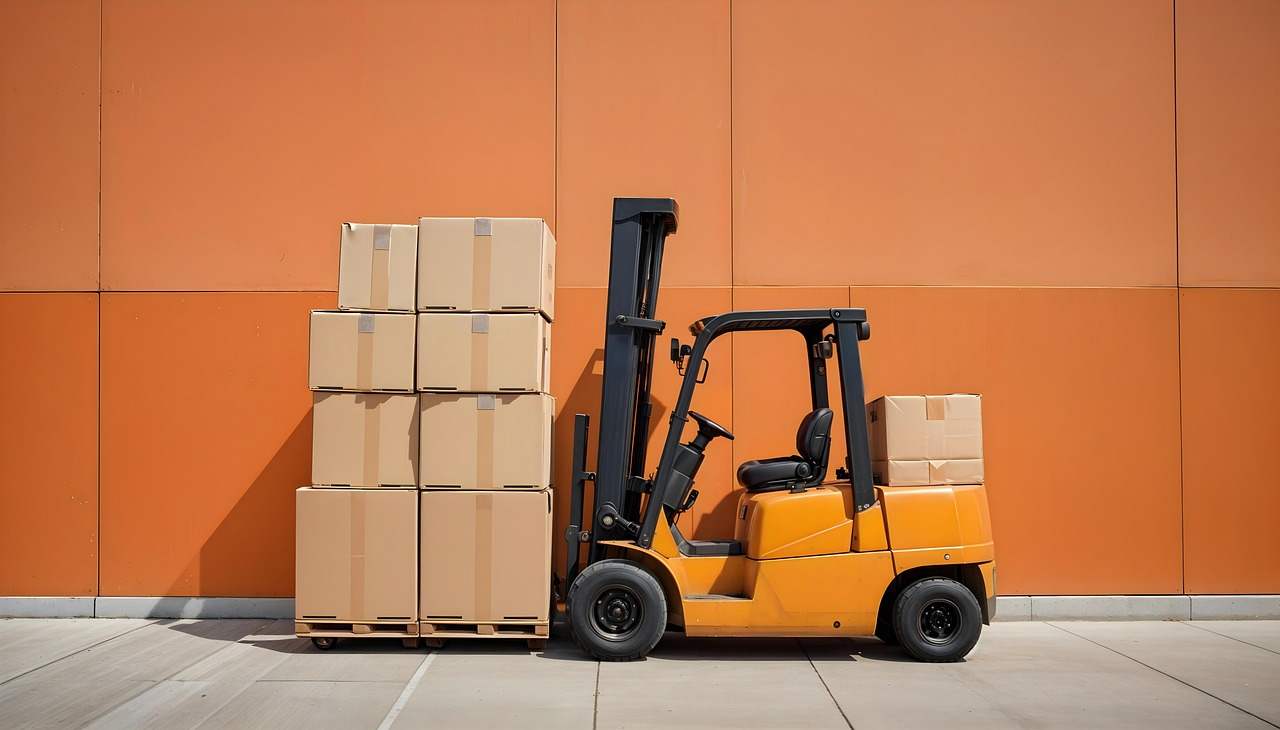
SOLUTIONS
We installed our real-time, data-driven Production Monitoring solution across the factory.
For every location, the process is to connect the machines to our gateways, set up a data pipeline to our platform, and create a dashboard for the client to visualize their data in real time. But that process has to adapt to its environment.
Getting plant-level data on the Gulf Coast is a hot, dirty job. Sometimes efficiency gains start in rooms full of loud machines with nooks and crannies full of dust and metal fragments in sweltering humidity.
The Special Projects Room was a particular challenge. Their two Haas CNC machines are connected together via a conveyor. Depending on the model of product being produced, they must run several unique programs and sequences. One model may have six programs, another may have three, and the model and sequence change all the time.
Each machine has the ability to make a whole part, but for flow purposes, one machine will run some of the milling programs for that part and send it to the other machine to finish. They follow a process where a conveyor moves the material into the machine, where it is clamped down, milled, and unloaded. At that point they can remove the finished piece, or send it to another machine via a conveyor to start the process over again.
Our challenge was to keep track of all of the programs between both machines to determine how many of each model was made. In addition to the model counts, we tracked the current sequence timing for each step (load, clamp, mill, unload), the total time, the average time for each step, and average time per part.
All of this data is displayed as a total and can be displayed by shift to see how many parts of each were made at which time. We overlay the counts with the daily goal of each part. We also monitor status at the machine level. Each of these machines have ~600 alarm messages. We loaded them all in and performed a pareto analysis to show which alarms came in, how often, and for how long.
RESULTS
We replaced their proliferation of OEM systems with a single point of data ingestion across brands and vintages.
The Glassdome platform provides a comprehensive log of what occurred throughout a shift that updates in real time. We also gave them the capability to calculate the number of specific parts made by shift.
This project is just the start. We’re also working on:
Incorporating time study data. The client has performed a time study which tells them how long it should take for each activity. We will compare actual production with expected time study. Each model and program has a unique time duration.
Incorporating maintenance checklists. Digitally record when these daily, weekly, monthly, semi-annually, and annual checklists were performed and by who.
Deploying a mechanism to log scrap quantities.
Tracking consumables usage. For example, how long it’s been between changing out cutting blades.
We’re also rolling out the solution at a second plant in Illinois.
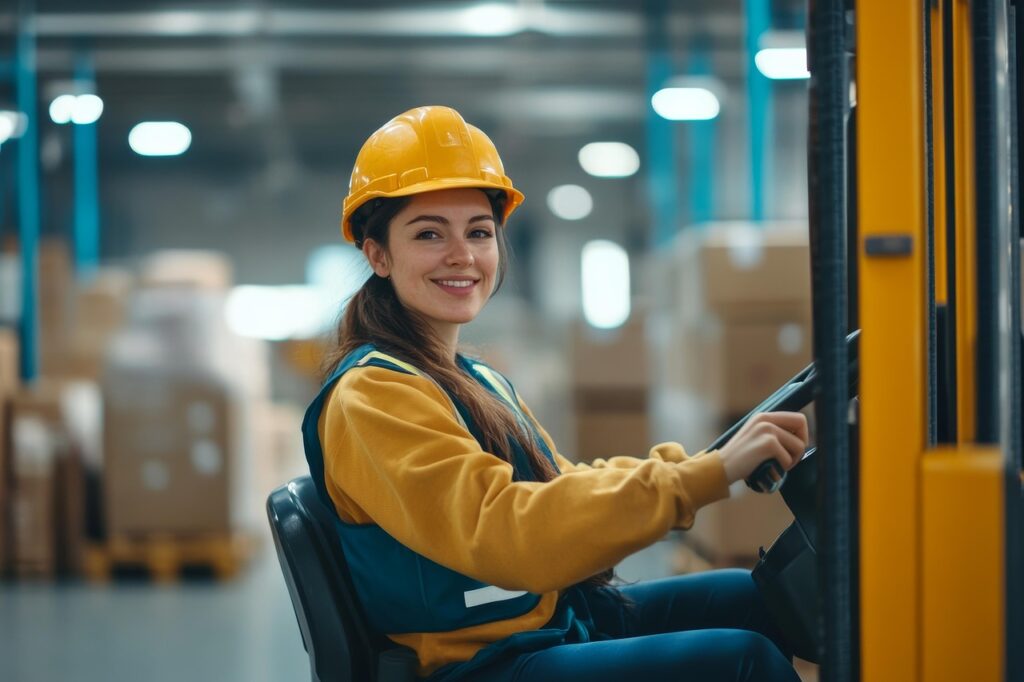
Production line reporting
BEFORE GLASSDOME
Manual data entry and reporting
AFTER GLASSDOME
Sitewide real-time visibility
Shift results visibility
BEFORE GLASSDOME
Long calculations based on manual data
AFTER GLASSDOME
Automated shift-to-shift reporting
POWER UP YOUR
MANUFACTURING EFFICIENCY AND CARBON REPORTING
