7 Reasons Why a Production Monitoring System is Important
By John Wright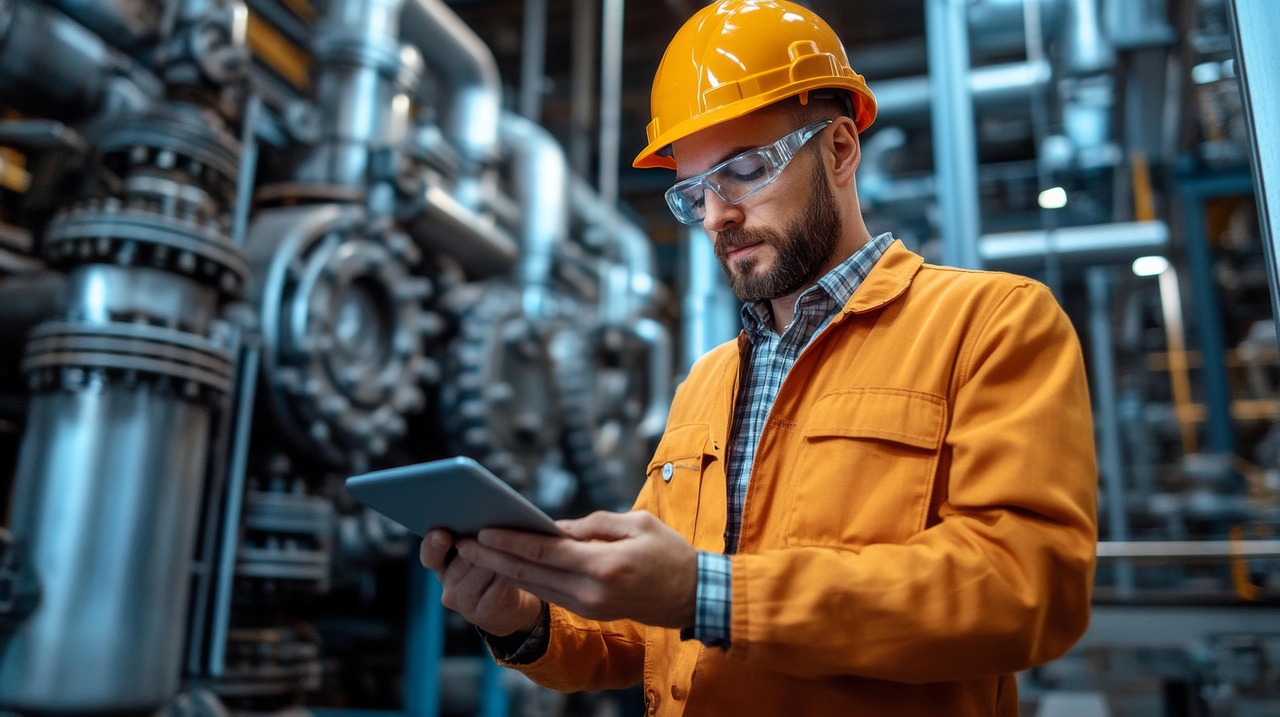
A production monitoring system takes factories from clipboards and dry erase markers to total process visibility in a flash. It’s more flexible and granular than a legacy MES or ERP system, and much less of a burden to install and update.
When it comes time to spend money on a production monitoring solution, plant managers and operations leaders need to justify their investment. It’s easier to say more machines equal more productivity, even though a machine costs many times more than a solution like Glassdome. Production monitoring makes your factory more productive for less money, it’s just a slightly more complex argument.
That’s why we’re showing you seven ways a production monitoring system can make your factory more productive.
1. Clear Visibility
Know what’s happening with your machines, production lines, and employees in real time.
If you can’t measure something, you can’t improve it. Production monitoring helps you use accurate data to cover every aspect of OEE, including downtime, quality, and speed.
We’ll cover it further on, but that visibility also means you can solve problems when they happen, and quickly spot bottlenecks and malfunctions.
2. Accurate Comparison
Timely, accurate, standardized data means you can compare machine-to-machine, shift-to-shift, line-to-line, plant-to-plant, or even region-to-region.
That helps managers set informed goals and standards and know what peak performance looks like.
3. Enhanced Efficiency
Visibility and standardization lead to more efficient facilities. A clear look at processes means a clear understanding of where bottlenecks, waste, and built-in downtime happen.
Standard data and documentation mean best practices and efficiency breakthroughs can be adopted across plants, and the employees responsible can be rewarded.
4. Faster Fixes
When a machine goes down, a worker steps away, or a technical system glitches, real-time visibility means the line can spot and solve the problem immediately. Instead of waiting until a disappointing number is written on a whiteboard, employees and plant managers can get the plant back running smoothly.
Faster feedback also helps ensure small issues don’t turn into big ones. Critical issues can be solved right when they happen, not when they cascade across the plant, and ultimately across supply chains.
5. Higher Quality (and Less Waste)
Production monitoring dramatically shortens the quality control feedback loop. Production monitoring systems provide a platform to collect and share data about products during the production process.
Integrating IoT systems like 3D cameras, temperature sensors, and weight scales only make those systems more productive and cut waste even further.
Glassdome’s IoT gateways interface directly with even the oldest or most esoteric machines, pulling real data in real time.
The result is less waste and a more consistent product.
6. Proactive Maintenance
Visibility in the performance and condition of your machines help stop unplanned downtime. With real-time data, you can see the health and performance of your machines and other assets at any time. Setting up alerts helps you know when something needs to be corrected.
You can set up smarter maintenance schedules based on run time rather than workdays. You get your oil changes based on how many miles you drive, not how many months it’s been. Why would you treat your industrial machines any differently?
Proactive maintenance can also cut planned downtime, reducing the amount of inspections necessary for properly functioning equipment.
7. More Satisfied Customers
A well-integrated production monitoring system helps you produce more products, of higher quality, on schedule. What customer doesn’t like that?
Once you have a good view of your data, you can use it to adjust production schedules, plan inventory, and create more informed employee schedules, all of which feeds into better, more consistent production.
When a customer continues to get what they asked for, when they ask for it, they become loyal, and even start telling other buyers in their network.
What should I look for in a production monitoring system?
You want a system that lets you see real data in real time, preferably at the machine level. If you want a really accurate view (and who wouldn’t?), you’ll want to make sure your system can integrate with every machine on your floor.
You should be sure that manufacturing experts will be there to help you install sensors, set up a data pipeline from your machines to the platform, and answer your questions and concerns.
The Glassdome Production Monitoring solution handles all of that and more. It’s a powerful production monitoring platform and efficiency improvement tool, and it comes at a price that’s a rounding error next to a new machine.
Export to or from Europe? You can handle your EU carbon compliance with the data your production monitoring system collects. The Glassdome Product Carbon Footprint platform turns your real data into automated, ISO 14067 verified reporting.
Ready to see the rewards of total visibility?
Get in touch with a Glassdome manufacturing expert